Resilience, Pace and Futureproofed Building Solutions
Designed for resilience, delivered at pace and fit for the future, The Ministry of Justice (MoJ) has long-chosen to use Premier Modular’s offsite solutions to meet a range of building needs for projects across the UK.
Premier has worked with the MoJ for over two decades, on numerous projects, including a number of joint ventures with tier one contractors, developing NOMS (National Offender Management Service) and BREEAM (Building Research Establishment Environmental Assessment Method) compliant/excellent solutions.
Each project’s modular solution was designed in close collaboration with contractors and clients to deliver high-quality spaces, which meet a range of different uses, including:
- Police custody suites, including secure holding cells
- Houseblocks, including steel-framed prison cells and ensuite facilities
- Healthcare facilities on prison sites
- Educational facilities
- Sports facilities
- Halfway housing
- Visitor buildings
- Office spaces
- Onsite catering facilities.
Reducing security concerns and speeding up programme times
For the MoJ, there’s a number of benefits to each of these facilities being delivered offsite – primarily, reducing security and disruption concerns onsite and programme times for the overcrowded estate, alongside creating value for money solutions with a high percentage of build manufactured offsite in a highly-efficient manner.
As all buildings are manufactured in a controlled factory environment, there’s less security cleared personnel needed onsite for extended periods of time. Alongside ensuring robust quality with Cat C level security, this also minimises the impact of unfavourable weather conditions on the projects’ planned timescales, reducing delays and overall programme times by up to 50%, when compared with traditional, in-situ construction methods.
The certainty offered by offsite factory manufacture also enables budgets to be more strictly adhered to, as there are fewer unknown quantities and delays throughout the build programme and budgets.
Energy-efficient and sustainable solutions
For every modular solution, Premier is focused on creating sustainable spaces. In its controlled factory environment, every modular building benefits from lean manufacturing processes, with low-carbon emissions and zero waste to landfill, reducing the project’s environmental impact.
A number of Premier’s MoJ projects have also achieved BREEAM ratings of Excellent, which sets the standard for best practice in sustainable design, measuring a building’s environmental performance. One project, which involved the manufacture and delivery of new houseblocks for a young offender’s institute, received a BREEAM score of 76.23%, alongside a BREEAM Award in the Prisons category.
By aligning individual building designs to client sustainability goals, Premier also supports its clients’ net zero ambitions through solutions. For example, by producing spaces with improved airtightness and U Values and making the most of modern, green technology, such as photovoltaic (PV) solar panels and air source heat pumps.
Premier’s offsite solutions are also fully reconfigurable, meaning that once installed, they can be adapted easily as use needs evolve.
Case study: Category C prison in the East of England
This men’s Category C prison, operated by His Majesty’s Prison Service (HMPS), needed a number of non-custodial facilities as it increased its capacity to accommodate a rising prison population.
Premier Modular designed, delivered and installed three new 2-storey buildings, which provided a range of facilities to enable the prison’s seamless operation as it expanded:
- Building one: 1,307m2 healthcare building, including dentistry facilities
- Building two: 1,900m2 visitor buildings, with office spaces for prison staff
- Building three: 750m2 kitchen building, with high-spec, commercial, secure catering facilities.
Using offsite, lean manufacturing, the project was taken from concept to completion in just 28 weeks, meaning the prison was able to mobilise quickly to accommodate an increased number of offenders.
Each of the buildings was manufactured and certified to meet Cat C security level requirements. Secure fencing was used to segment the installation areas from the main prison, keeping security risk levels low throughout.
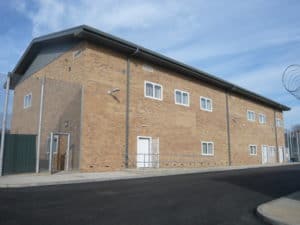
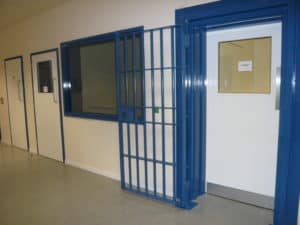
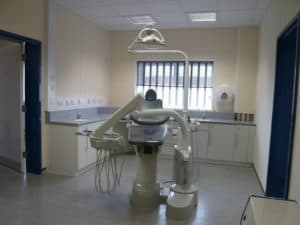
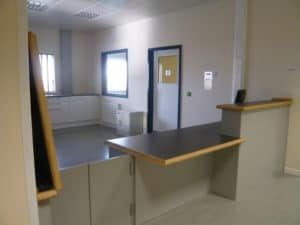
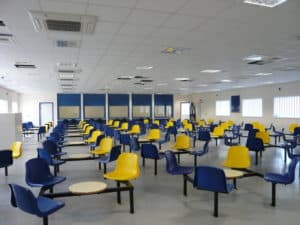
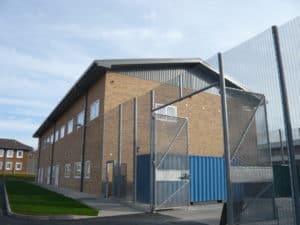
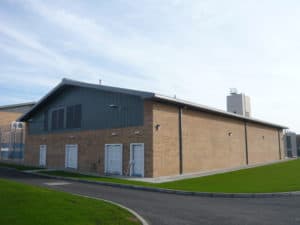
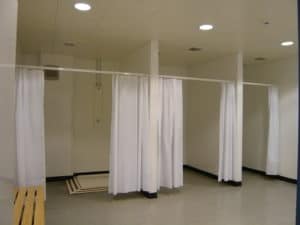
Case study: Young Offenders Institution in the South East of England
This male Young Offenders Institution, operated by HMPS, was nearing capacity and facing significant pressure to expand quickly to accommodate its rapidly increasing offender population.
Selected for its innovative building design and ability to deliver quality solutions at unprecedented pace, Premier, alongside a key contractor partner, developed and installed a Cat C certified 240 place prison extension from three cell houseblocks, with a site programme time of just 12 weeks. This included:
- Education and teaching block
- Visitor’s centre
- Healthcare facility
- Sports changing facility
- Gatehouse.
To ensure site security and reduce risk, all onsite installation works were surrounded by secure fencing. With sustainability an integral consideration for the new building, Premier prioritised environmental performance in its design and manufacture, which resulted in Premier and its contractor partner winning a BREEAM award in the Prisons Category, after the houseblocks achieved a score of 76.23%.
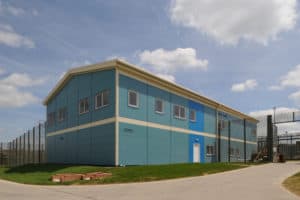
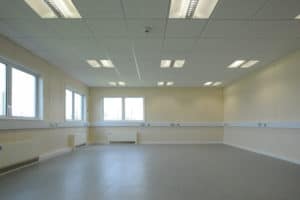
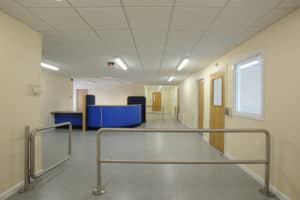
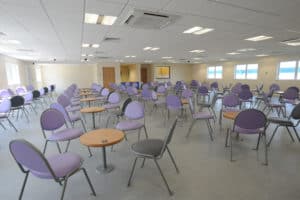
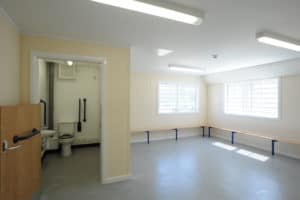
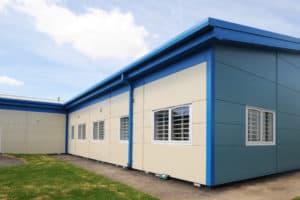
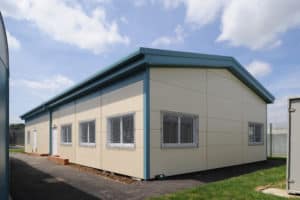
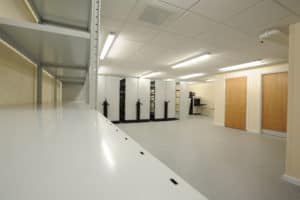
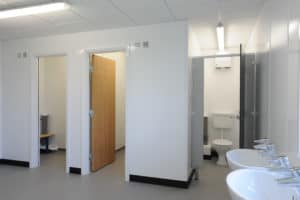
Case study: Category C prison in the East of England
Like many prisons, this Category C male prison, operated by HMPS, was facing pressures to increase its capacity rapidly to account for its rising offender population.
Premier designed, manufactured and delivered a total of 480 Cat C certified cells, which formed four 2-storey, 120-cell houseblocks.
Offsite construction meant every building component was manufactured in Premier’s controlled factory environment:
- Roofs
- Services
- Walkways
- Cells (at a rate of 40 cells per month).
This meant the installation phase was a rapid assembly process, minimising disruption by reducing time onsite. The overall rapid-build solution was delivered in just 39 weeks, from concept to completion.
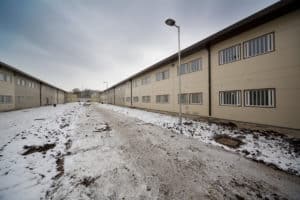
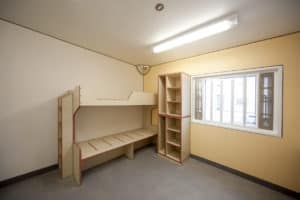
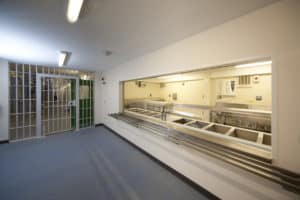
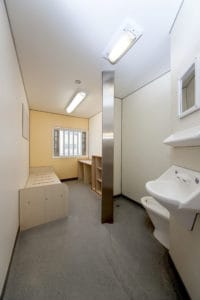
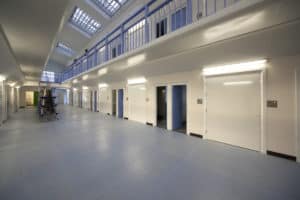
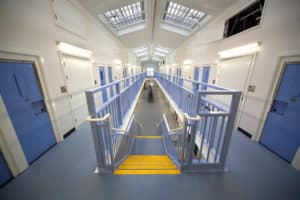
Cost-effective solutions
Premier’s extensive supply chain experience and knowledge of MoJ best practice build, means we’re able to develop solutions that demonstrate value for money for our clients. Our modular buildings can be purchased or leased for short or long-term use, depending on individual requirements and budget constraints.
Right from the initial concept stage, Premier works closely with the MoJ and contractor teams to ensure the design is fit for purpose, ensuring budgets are met, while still meeting client needs.
Performing to the highest security standards
Of course, for the MoJ, security is paramount – and its buildings need to meet some of the highest security standards in the world.
As a result, every member of the Premier site team is regularly subjected to some of the most scrutinous checks and training to ensure they’re able to work effectively and safely on the high-security sites. It also produces its modular solutions with several key security considerations, including enhanced steel-framed structures.
Offsite – designed for resilience, delivered at pace and fit for the future
Minimising disruption is critical to ensure maximum safety and security for MOJ sites – which is why offsite solutions work so well.
Or, if you need support with a project, get in touch