Premier Modular’s permanent division has recently completed a £10m project for Ashford and St Peter’s Hospitals NHS Foundation Trust. We were chosen as the primary contractor, working alongside delivery partner, Claritas, for the 62-bed priority assessment facility at St Peter’s Hospital in Chertsey, Surrey.
The Trust needed the new structure to accommodate rising demand, especially during the busy winter season. St Peter’s chose an offsite solution to fast-track the building project, which decreased programme time by nine months.
Solution-led design
Carefully designed by BDP and delivery architects P+HS, the new space seamlessly integrates into the existing building, as its design mirrors the original building’s environment, while meeting the hospital’s modern needs.
Connected to the existing hospital building’s emergency department, the new facility offers 62 patient bays, as well as nursing stations, staff rooms, seminar rooms, laundry and clean utilities and staff kitchenettes. It also incorporates modern technology, with datacomms, security systems, CCTV and nurse call systems, which are fully integrated with the main hospital building.
“This project shows how striking and unique architectural design, that is also in keeping with its surroundings, can be successfully married with efficient delivery via offsite construction, bringing many benefits including speed and quality,” states Akshay Khera, architecture director, BDP.
The offsite solution was developed to fit perfectly with the existing hospital, maintaining traffic flows between the old and new units, with consistently level floors throughout. The assessment unit is finished externally with grey vertical rainscreen cladding and brickwork to match neighbouring structures.
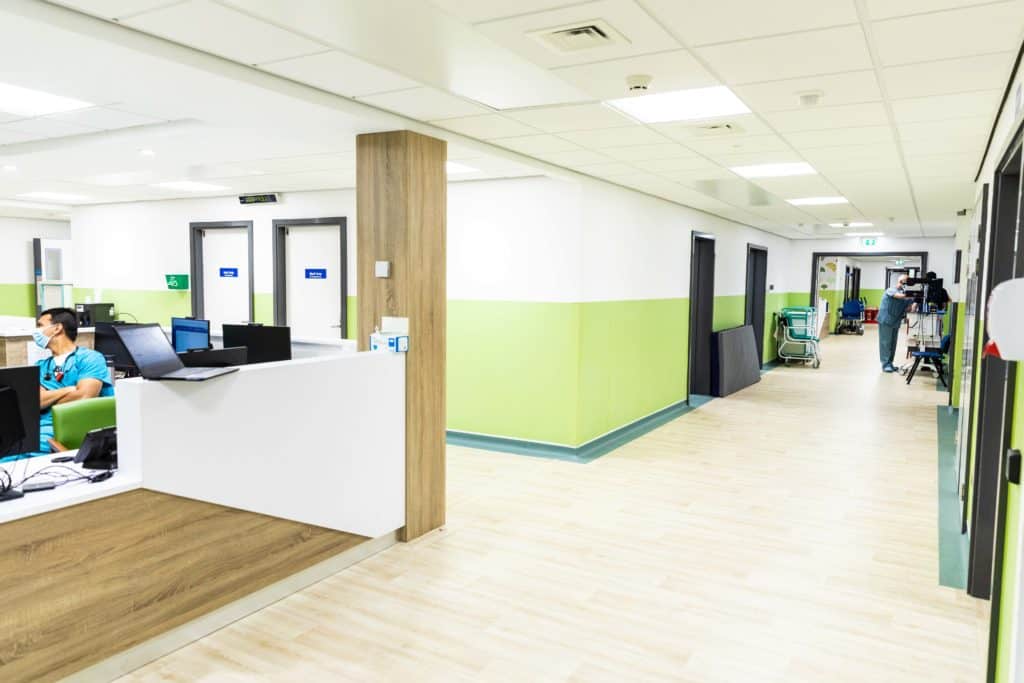
A sustainable future
The building envelope is constructed to be thermally efficient, lowering operating costs and carbon emissions, to support the Trust’s sustainability goals. It uses technology to optimise energy use, including solar control glass, brise soleil sun shading and a building energy management system (BeMS).
Technical expertise
Andrew Grimes, assistant director of property and capital development, said: “This project responds to the urgent national need to increase capacity in emergency care. Offsite construction allows us to add space on our hospital campus more quickly. We estimate Premier reduced time on site by around six months and the overall programme by nine months. Less time on site also means less disruption to patient care, which is always a priority for hospital building projects.
“Premier had the capabilities to meet the technical constraints of this site and the brief very well, particularly to provide seamless connections at two levels to maintain patient flows and allow us to move beds easily between this building and the existing facilities. Premier was also the only offsite specialist who was able to meet our module height requirement without the addition of ramps. And the lightweight nature of steel-framed modular construction minimised groundworks which had time and cost savings.
“Premier demonstrated the flexibility and design capabilities to engineer a bespoke solution for this challenging site, with all the speed and value benefits of offsite construction,” concludes Andrew.
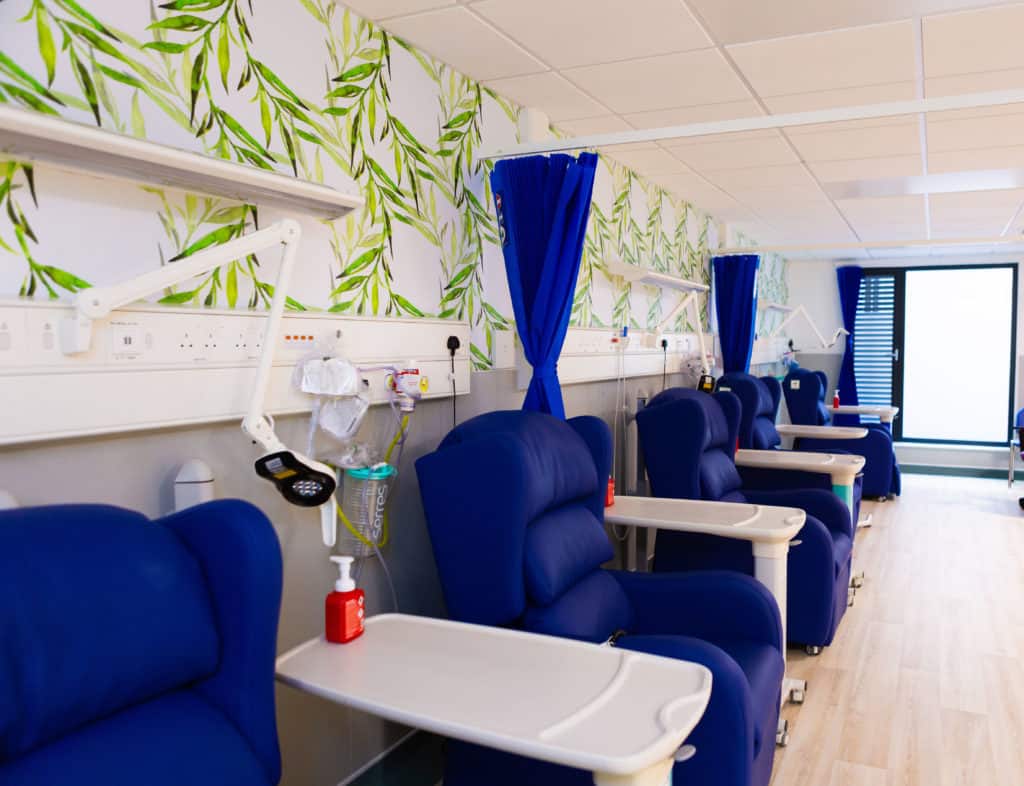
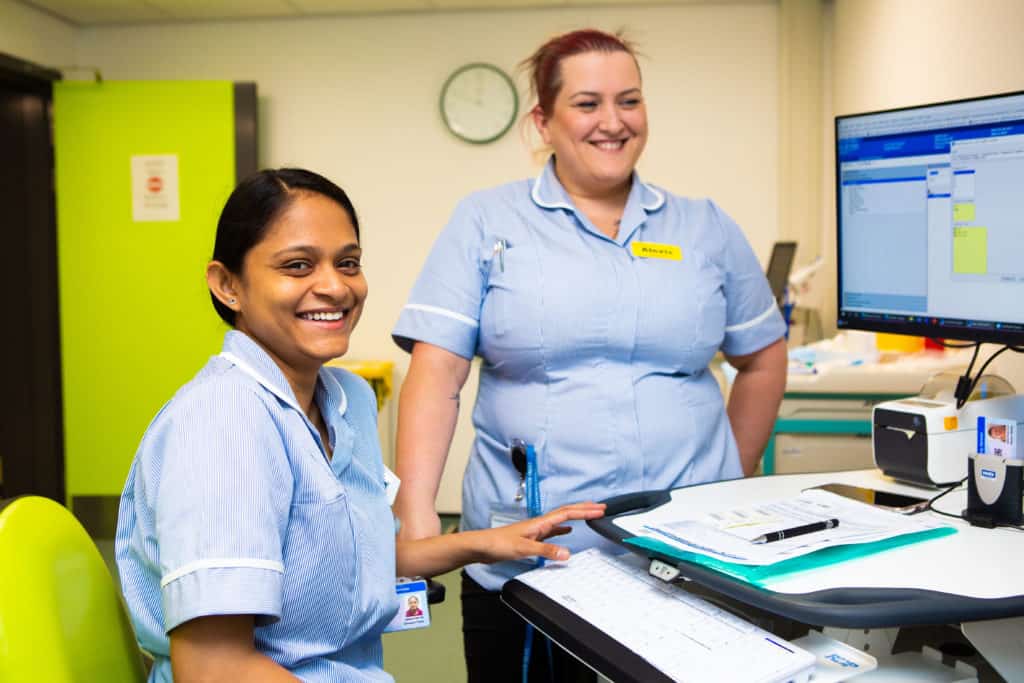
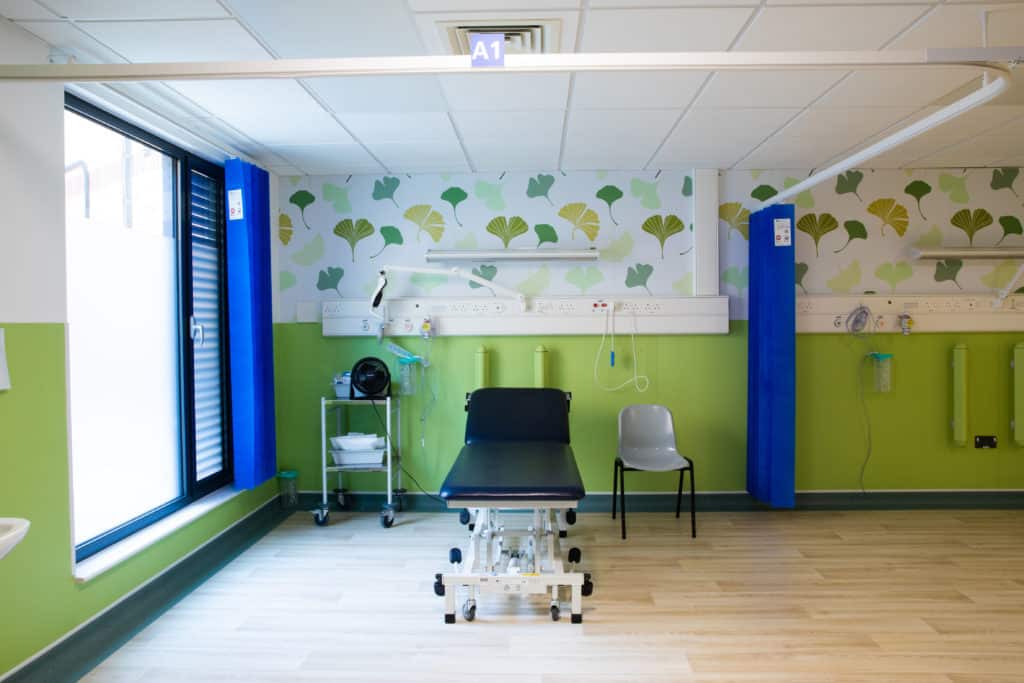
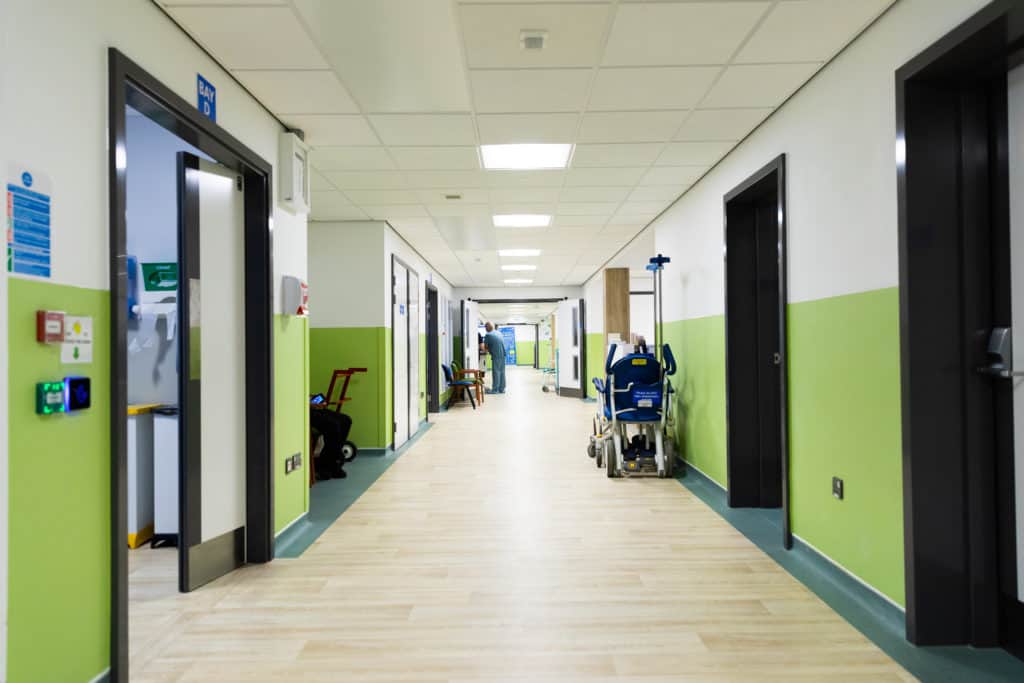
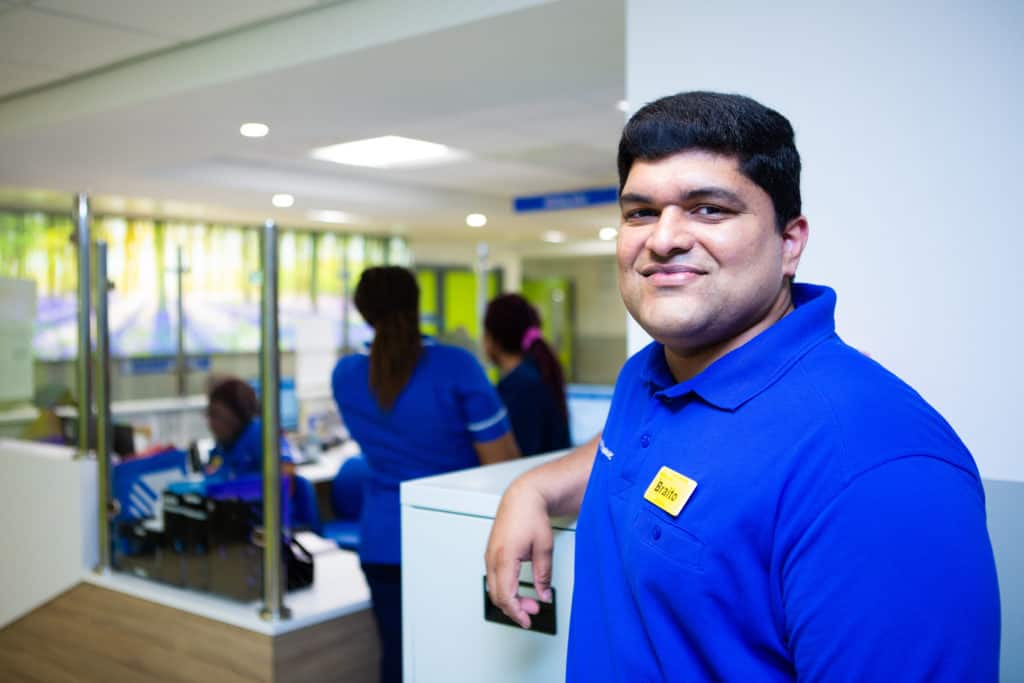
Specialist healthcare expertise
“This scheme was ideally suited to offsite construction. It allowed the Trust to meet an urgent need to expand capacity for emergency care and the development of a very constrained site,” says Dan Allison, divisional director, Premier Modular.
“The new building has been constructed in a courtyard and close to the emergency department, which required careful logistical planning from our project team. We maximised construction and fitout work offsite to radically reduce disruption to patient care and were only on site for around six months to produce a facility for the trust.”
At Premier, we create sustainable environments for people to live, learn, work and care for others through bespoke modular buildings, for all types of hospital sites. We’re always up for the challenge – thanks to our technological proficiency, dedication to sustainability and pace. For more information on our modular healthcare facilities, get in touch or call 0800 316 0088.