The construction landscape is changing for the better. As an industry, we’re driving for greater efficiency, flexibility and sustainability – and modular building is positioned perfectly to deliver all three – and more.
In this blog, we talk to Premier’s MD, David Harris, who explains:
- What’s changing
- How modular is evolving
- How Premier is keeping one step ahead of the curve by delivering sustainable spaces that create a better tomorrow, every day, for future generations.
Q: Can you start by giving us an insight into today’s modular marketplace?
A: The modular building marketplace has grown exponentially over recent years, as customers look for solutions that are more efficient, sustainable and represent value for money, without compromising quality.
As the traditional construction industry battles with labour shortages and resource challenges, it’s increasingly difficult for these companies to hold contract durations and prices. Meanwhile, the modular building industry is thriving.
In our factory, we have access to a full range of skillsets for different projects, it’s a controlled environment with clearly-defined manufacturing processes to reach a high-quality end solution, on time and within our clients’ budgets.
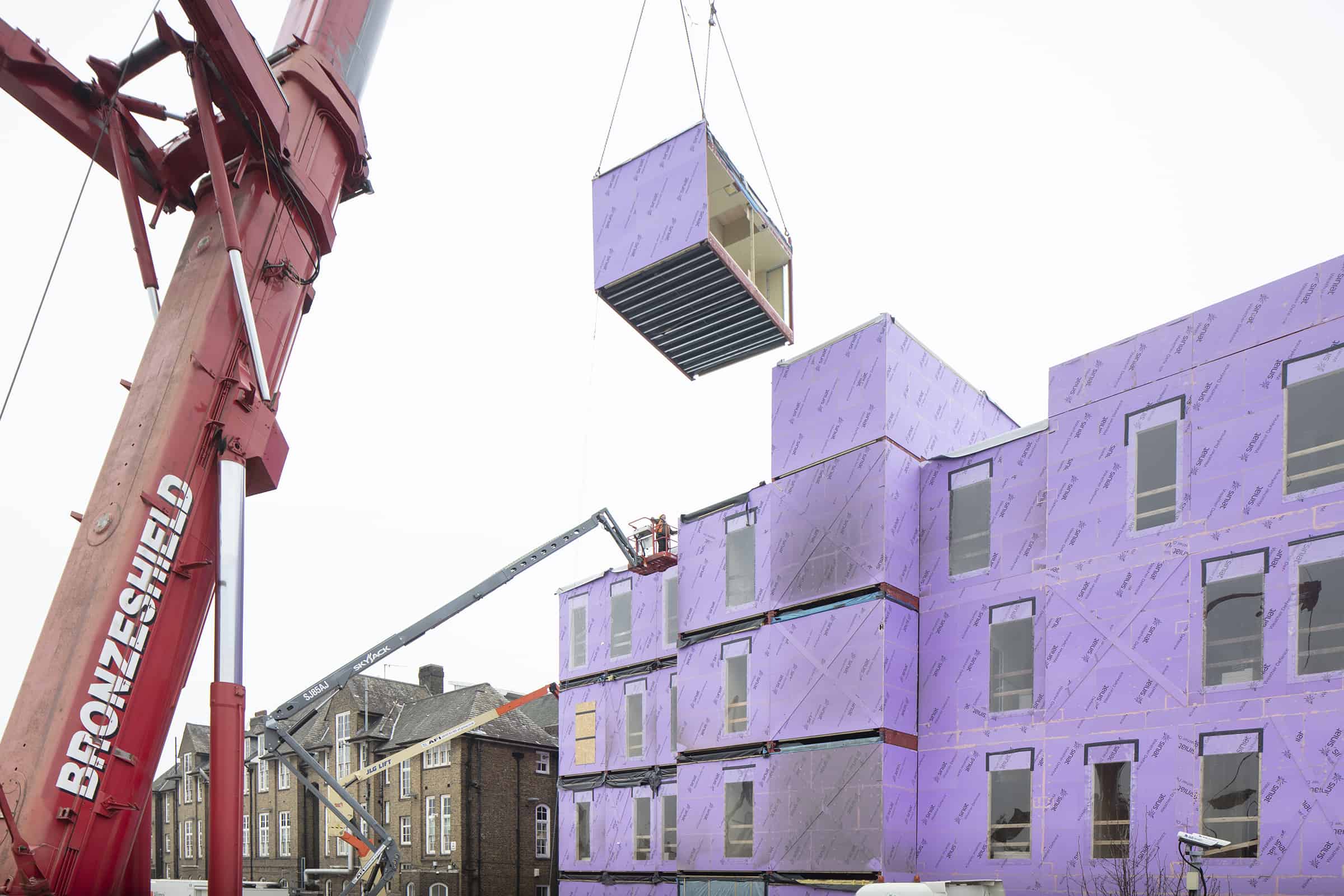
Q: Are there any significant challenges facing the construction industry as a whole?
A: Over the last decade, business generally has seen some of its toughest challenges: Brexit, COVID, the Ukraine war, the energy crisis, inflation, exchange rate challenges, etc.
Overcoming each of these challenges needs a different approach, but the common factor in beating them is the ability to adapt – quickly.
For example, during COVID, we adapted our processes almost overnight to ensure hygiene control and social distancing throughout our manufacturing process, which enabled us to remain open throughout the pandemic, without losing a single day in our factories.
Q: How is modular building helping to overcome these challenges?
A: Lending itself to lean manufacturing, modular building offers an alternative to traditional construction to achieve high-quality permanent structures – more efficiently, sustainably and cost-effectively.
Arguably, the most important of those in today’s world is sustainability. That’s what we’re always driving for in whatever we do. We generate zero waste to landfill in our factories and produce sustainable spaces through our buildings by maximising energy efficiency.
Our modular buildings are fully flexible, reusable and reconfigurable. That means our clients are able to adapt their buildings to changing needs, shifting demographics and to meet decarbonisation goals.
Modular methods also minimise onsite disruption, which is key for the majority of the industries we work in, such as healthcare and education, creating significant advantages for the environment, quality, safety and programme reduction.
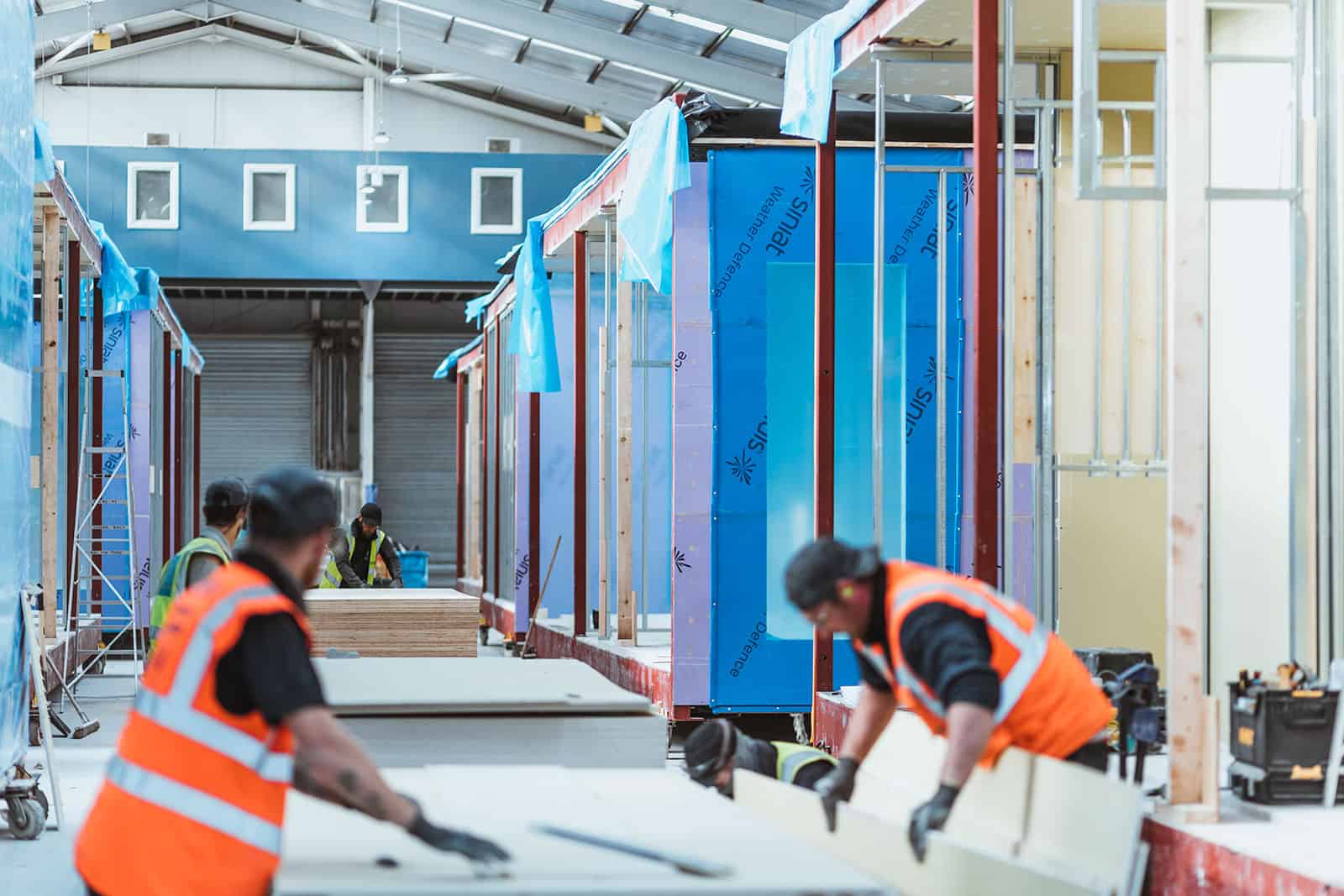
Q: How is modular building changing?
A: In so many ways. At Premier, we’re focused on continual development, by investing to advance our capabilities even further. In recent years, that’s involved:
- Digitisation/BIM, which focuses on information flow from project inception to handover and life in use.
- Improving our business systems with an enterprise-wide ERP system to enhance our processes across every department.
- Investment in skills/training:
- In our existing team as we grow – training at every level throughout the business, whether that’s putting people through MBAs or technical degree support, for example.
- In our future team – through our ‘Premier Academy’, which launched at the start of 2022, and has already tripled our annual apprentice intake, enabling us to train more local young people into the industry.
- Ongoing product investment, which has seen us invest heavily into new products for our clients and new factories to support our expansion.
Q: You mentioned earlier sustainability was incredibly important across the whole industry, how is Premier bringing that to life?
A: As a business, we’re committed to being net zero in operation by 2035. Premier Modular Group recently acquired Net Zero Buildings, which specialises in delivering sustainable spaces that reduce the impact of construction on our environment.
In the construction industry, so many people are ‘talking’ about net zero and sustainability, but not many are actually ‘doing’ much about it. Net Zero Buildings is taking on that challenge with technology to make a difference for generations to come. We have just handed over two projects, both net zero in operation: Hart School and Treetops Free School. Treetops was the DfE’s first net zero pathfinder school.
As a business, we have also recently launched a ‘carbon calculator’ to support our clients’ options to reduce carbon in operation in their buildings. We have launched this initially within our rental solutions, and it has been very well-received.
We’re currently installing photovoltaic panels and running trials with electric fork lift trucks at our main factory.
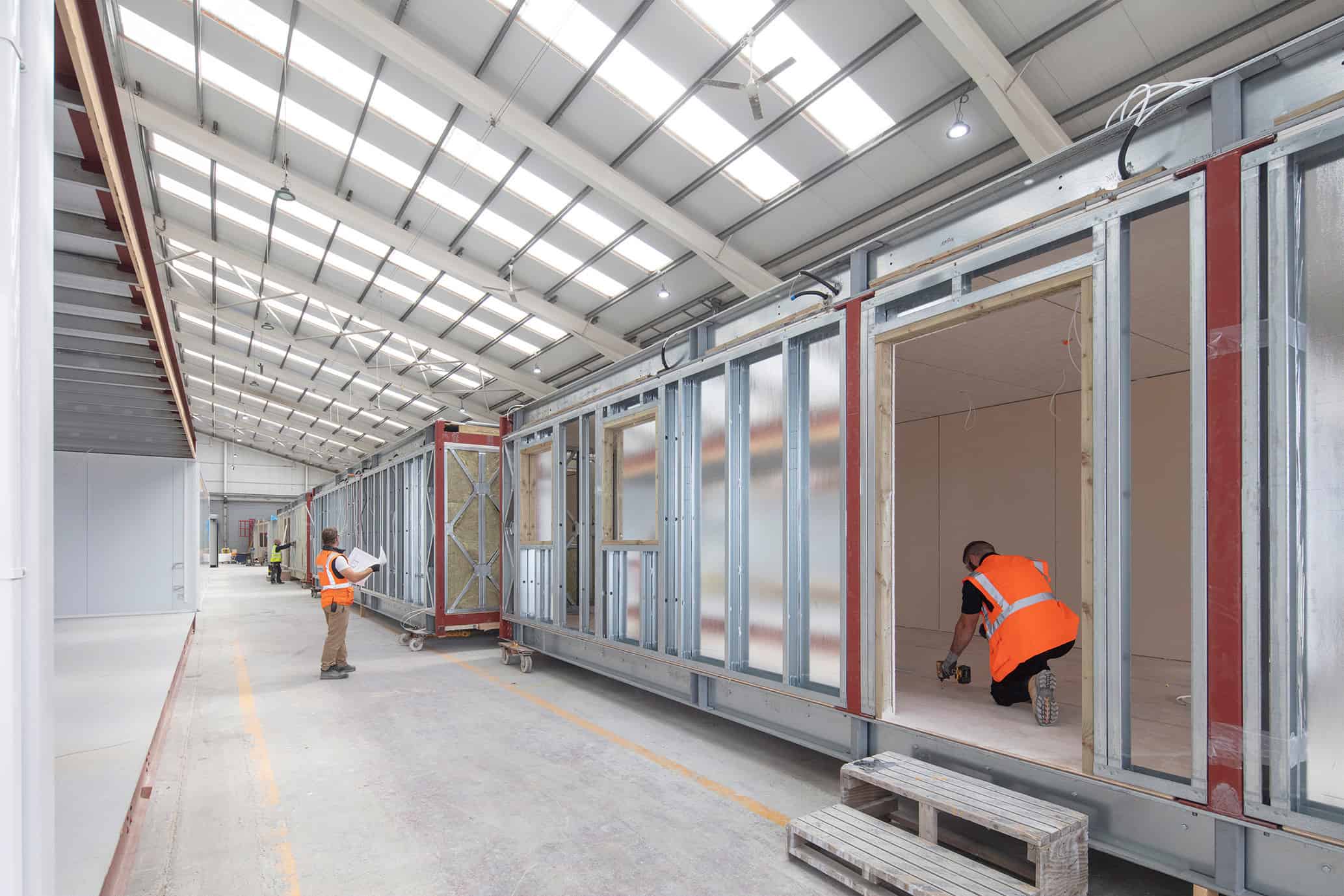
Q: What can we expect to see from Premier over the next 2-5 years?
A: As the construction industry searches for more sustainable building solutions, there’s a clear opportunity to expand and develop modular/offsite, both across the UK and into Europe.
Our focus at Premier – both now and over the coming years – is to remain a top three industry player, by expanding into northern Europe and continuing to show the world how modular is the answer for our buildings to achieve net zero.