Modular buildings are fast emerging as one of the best ways to reduce the staggering carbon footprint of the construction industry.
Building design and solutions must advance and develop with NHS healthcare services as they continue to change.
Premier Modular collaborated with the King’s College Hospital NHS Foundation Trust to help supply more modular space, allowing the Trust to maintain effective patient care during its expansion. See how King’s College’s latest project has addressed foreseen healthcare developments, setting an example for the sector.
Trend 1 – creating more space to relieve waiting times
NHS Trusts must meet waiting time reduction goals, which frequently call for adding or enhancing facility capacity.
A brand-new, four-storey outpatient unit was required by King’s College Hospital to assist with this.
They decided to choose an offisite modular option for a number of reasons:
- Compared to a traditional brick and mortar build, the original construction schedule was cut in half. Groundwork was done simultaneously whilst the building’s construction was undertaken in Premier’s state of the art factory
- Minimal on-site disruption – it was essential that the emergency helicopter remained in operation during install.
- Each floor was opened independently, meaning two new floors could be used prior to the completion of the others.
King’s College’s estate and traffic management team worked together with Premier Modular to plan the building’s installation to minimise any disruption to the hospital’s round-the-clock A&E services. Modular were installed during periods of low occupancy to reduce disruption to patient care.
Trend 2 – providing technical design solutions for a synergised and sustainable environment
Hospitals that utilise contemporary and durable modular architecture provide the same comfort and features, including acoustics, as those with traditional brick and mortar construction, but without the need for multiple craftsmen onsite or the protracted build schedule.
The most demanding and dynamic healthcare facilities are now opting for offsite construction and the flexibility to evolve that comes with this. Modular building can meet the most complex of requirements, such as operating theatres, yet can also be reconfigured and spaces repurposed to futureproof the buildings lifespan.
To improve service continuity and patient flow, a seamless connection between the original building and the new King’s College building was essential. Given that floors have a significant influence on how we evaluate buildings, the project’s floor plan was essential in addressing this need.
A key element of the design of King’s College was its GIFA floor. A GIFA floor was created with certain floor dynamics in mind, including how it will react to foot traffic, as well as other types of traffic, such hospital trollies.
High-quality gypsum fiberboard, or GIFA, was layered on top of a plywood foundation. GIFA boards can be installed over joists without the requirement for a subfloor, since they have tongue and groove edges.
The new GIFA flooring at King’s College was suitable for its surroundings and saved time and money by not needing to wait for concrete to cure. In contrast to using concrete, the units were operational in days as opposed to weeks.
All of the steel used in Premier’s floor frames and cassettes is recyclable. Without sacrificing performance.
Many NHS Trusts choose to fund their structures from operating expenses rather than construction expenditures, since modular buildings may be modified or recycled as requirements change.
This offers a sustainable solution as all of the materials utilised in this factory-building process are recyclable or reusable, with zero waste going to landfill.
Trend 3 – increasing energy efficiency
The new NHS Net Zero Building Standard, which aims to reduce the U-values of healthcare facilities and make them more airtight and energy-efficient, must be adhered to by every NHS Trust from 2023.
The NHS must use contemporary technologies to lower U-values, including mechanical, electrical, and plumbing (MEP) systems, air source heat pumps (ASHP) and air handling units (AHU), all of which are significantly reducing energy consumption.
A building management system (BMS) connected to mechanical and electrical (M&E) services allows for cost-effective energy usage control, since it optimises energy use based on operating hours and light or heat gain efficiency.
The most frequent source of natural heat entering healthcare structures is solar gain, and the BMS counteracts this heat with air conditioning and natural ventilation. Based on information from PIR (movement/motion) sensors, intelligent programming balances a hospital’s energy use with the occupancy of its buildings.
The new modular structure at King’s College not only satisfies present healthcare requirements, but it is also well-positioned to continuously enhance its operations and patient care. The system will be adjusted to allow those cost savings to compound.
The new structure has received the BREEAM ‘Excellent’ certification, checking off criteria including decreased energy use and carbon emissions.
King’s College will have a considerable decrease in carbon emissions (48.16%) in order to reduce energy use, with:
- A system that uses very little energy and provides precise heating and cooling
- Photovoltaic (PV) solar panels, an effective radiant panel system powered by air source heat pumps will provide about 45kWp of electricity.
Determining the right sustainable solution
Many NHS estates are located in busy environments and have been constructed over decades or centuries – resulting in a variety of types of structures.
The key to adding a new building to an NHS estate is early engagement with key stakeholders, both clinical and non-clinical, to determine project requirements, times schedules and budgets.
It’s crucial that the NHS collaborates with experts at this early stage, to explore technically led design and manufacturing processes for seamless offsite construction, efficient install and employ renewable technologies to embrace sustainability.
The future
Modern methods of construction (MMC) continue to grow as a preferred choice for NHS trusts, with streamlined project times, reduced time on site and disruption to patient care kept to a minimum. Creating high quality, open span spaced which can be reconfigured and evolve with the healthcare requirements yet still providing a safe and practical environment for patient and staff welfare.
The issues faced by NHS Trusts are frequently resolved by modern construction techniques. Groundwork takes place concurrently with the building coming together in the factory while building offsite, increasing the construction schedule. All of this works together to ensure that NHS services are uninterrupted.
For more information call 0800 316 0888 or email us at hello@premiermodular.co.uk.
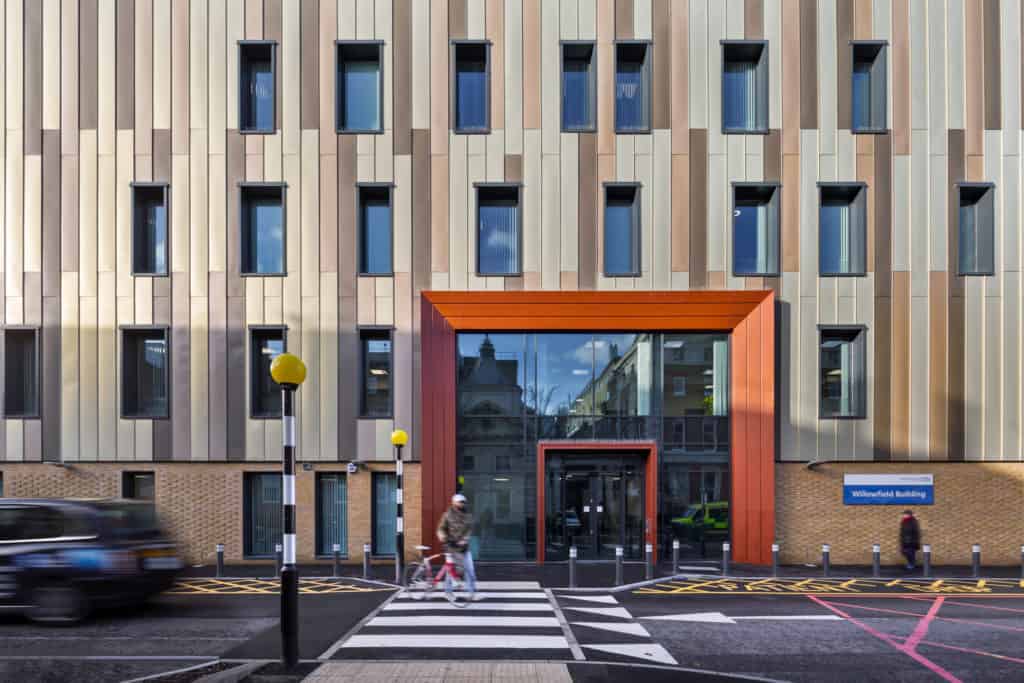
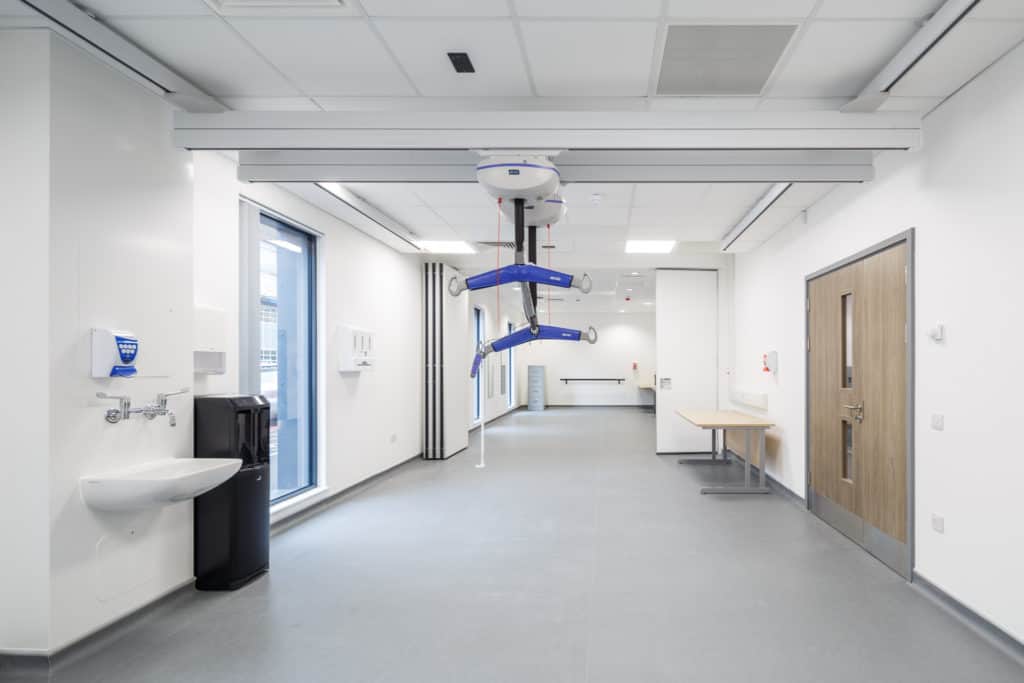