With the construction industry facing a rise in complicated outputs and strict deadlines, it’s imperative that infrastructure projects are completed to a high specification and within the planned timeframes.
Offsite production can support onsite personnel in an efficient, effective and sustainable manner while facilitating the timely delivery of vital infrastructure facilities and services.
Current trends in infrastructure
Speed of delivery is crucial, as infrastructure projects support the essential supply of facilities or systems needed by society, such as energy, transportation and science services.
A robust, contemporary society is built on a solid infrastructure. High quality projects not only supply top-notch services to those who depend on them, but additionally support economic growth and employment possibilities.
The main requirements for the construction of infrastructure projects in 2023 have been to meet sustainability goals and reduce environmental impact from the outset; maintaining this efficiency long after completion.
With the building sector responsible for 38% of the world’s carbon emissions, companies know that they need to act quickly. The sector must keep innovating and collaborating to stay on track as net zero targets approach and regulations surrounding sustainability expand.
Overcoming constraint and sustainability challenges
Many infrastructure projects include operating in confined spaces, such as alongside railway tracks, in close proximity to existing buildings or on nuclear power facilities. Access problems are frequent on such sites, often slowing down work and delaying completion. However, modular building allows for more effective and efficient delivery from contractors to keep infrastructure projects on track.
Delivering information quickly is crucial whilst working on restricted sites. Any delay in the workflow could have a cascading impact that ultimately pushes back completion. Offsite construction allows groundwork to be completed concurrently with building production, which takes place in a controlled factory setting, considerably reducing project programmes.
Modular structures provide a winning solution at a time when the value of sustainability is front and centre of both public and business consciousness. Sustainable Modular buildings can be moved to new locations and reused, or the structure recycled to reduce the embodied carbon of a building once it is no longer needed. Offsite manufacturing also results in less waste, due to the controlled factory conditions and precision engineering techniques. At Premier Modular, we produce zero waste to landfill.
Flexible funding and time optimisation
Modular construction has several advantages beyond just speed and sustainability. Businesses can take advantage of financial tools and frameworks that are designed to accommodate various spending limits and project-specific needs, such as LHC. Additionally, the rapid delivery and precise scheduling of off-site construction ensures effective project management and logistical planning, which in turn reduces the anticipated project time, as well as the number of subcontractors on site.
Fast-tracked infrastructure support
Case study 1: Supporting site teams working on HS2
Costain Skanska JV (SCS JV) needed welfare facilities and project offices for 15 sites along the track to support phase one of HS2, the new high-speed train connecting London, the Midlands, the North and Scotland.
Temporary building options that complied with fire ratings for facilities that would be in operation for at least five years were required to meet the needs of the SCS JV’s site.
Working with short schedules and extremely constrained locations near active railway lines required maintained communication with Network Rail in order to inform the extensive logistical planning, especially during building installation.
After four weeks of planning, more than 15,000 temporary buildings were provided, made up of more than 500 modules constructed to the exact needs and specifications of SCS JV.
The new structures benefited the wellbeing of the administrative and construction crews by providing:
- Open plan offices
- Meeting rooms
- Breakout spaces
- Drying rooms
- Toilets
- First aid rooms
- Canteens.
The structures’ lights, air conditioning, fire and security alarms, partitions and doors were all installed and functional in less than a day.
Numerous environmentally friendly measures have been proposed to lessen the impact of the new facilities, which are anticipated to be in use for at least the next five years, including:
- Rainwater harvesting – to provide water for site operations and personnel
- PIR lighting sensors
- Low water consumption showers
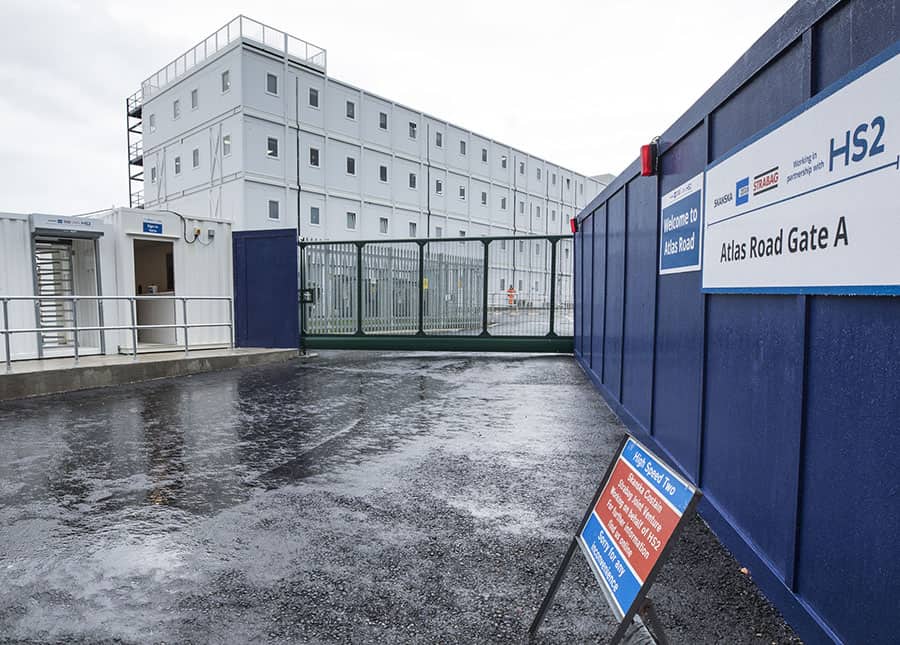
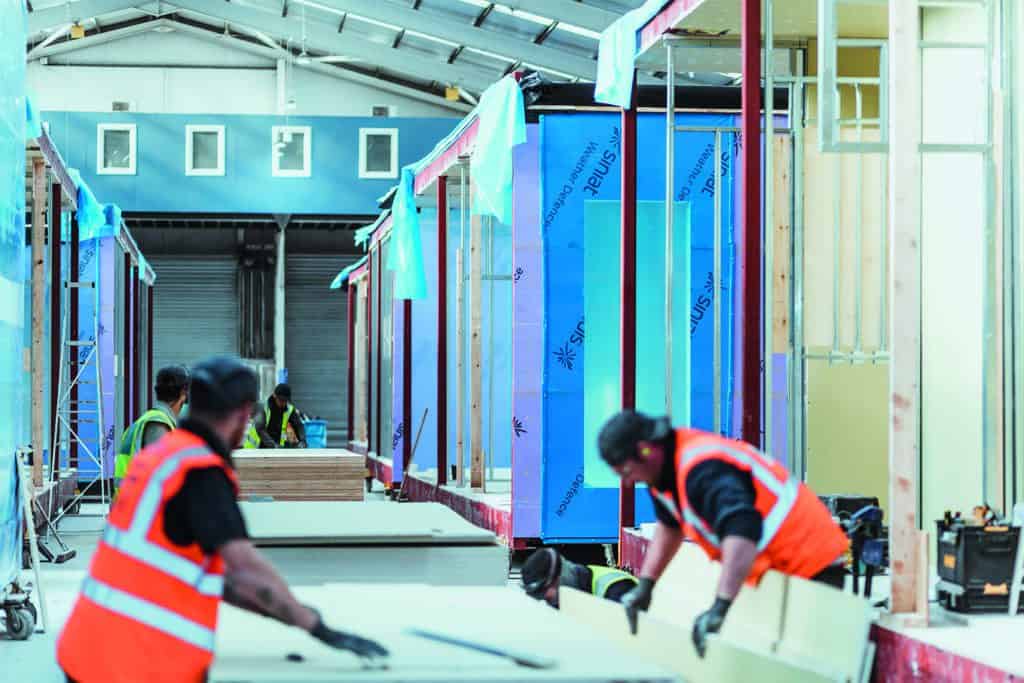
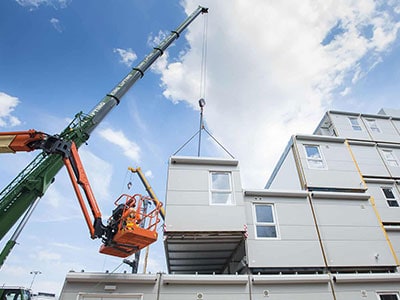
Case study 2: Boosting productivity at Wembley Stadium
For a residential development near Wembley Stadium, John Sisk needed office space and welfare facilities for its workers.
Construction requires a healthy and motivated crew, therefore it was critical that all health and safety procedures and regulations be followed.
The 2,710 four-story welfare building was prepared for use after a six-week site programme. The building’s 2.7m ceiling height gave it an open, breezy feel that made for a comfortable working environment. For ease of accessibility, the building was constructed with two outdoor staircases, one interior staircase and a platform lift. Facilities to promote the productivity and well-being of construction workers included:
- Changing and drying rooms
- First aid facilities
- An induction room
- Office space
- A canteen area with a commercial kitchen
- Meeting rooms
- Toilet facilities.
John Sisk’s teams were able to be on site right away and start building thanks to the tight delivery schedule, which helped them finish the project on time.
An observation deck was installed on the building’s roof as additional benefit for the project managers and the marketing division, allowing for an incredible site view.
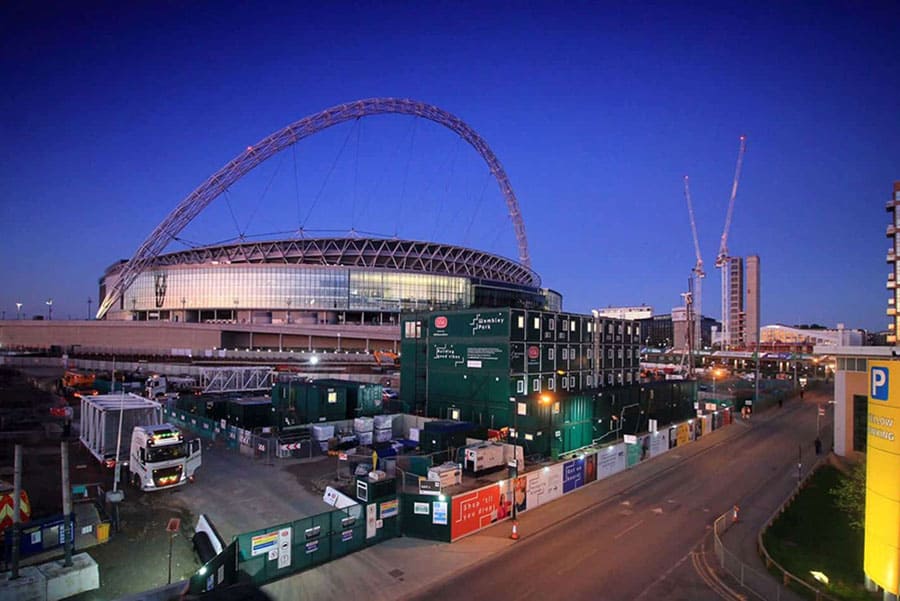
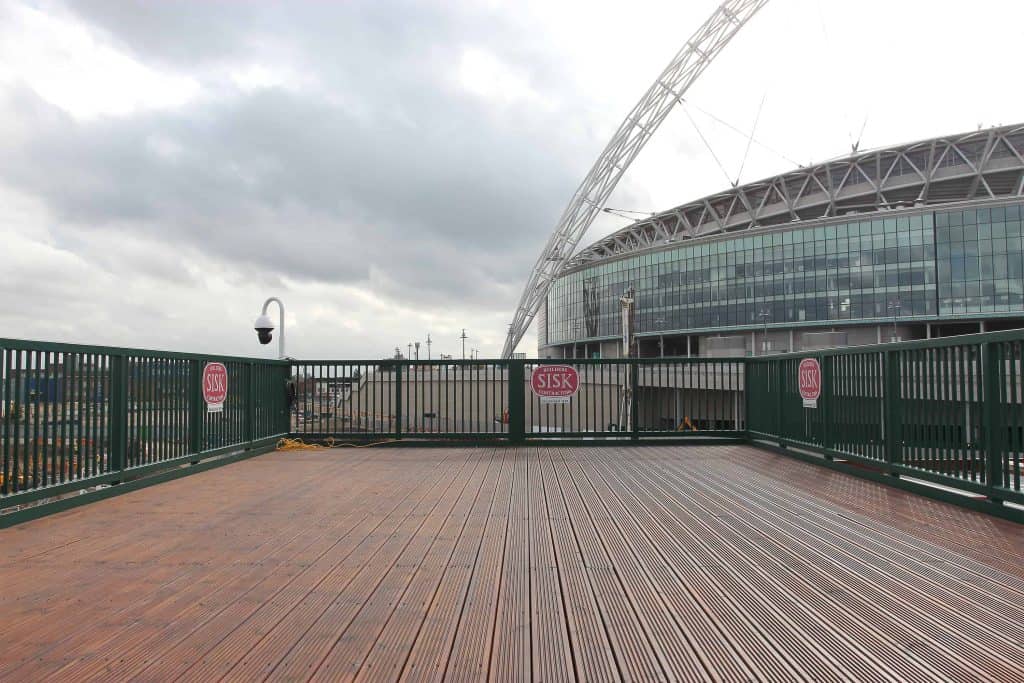
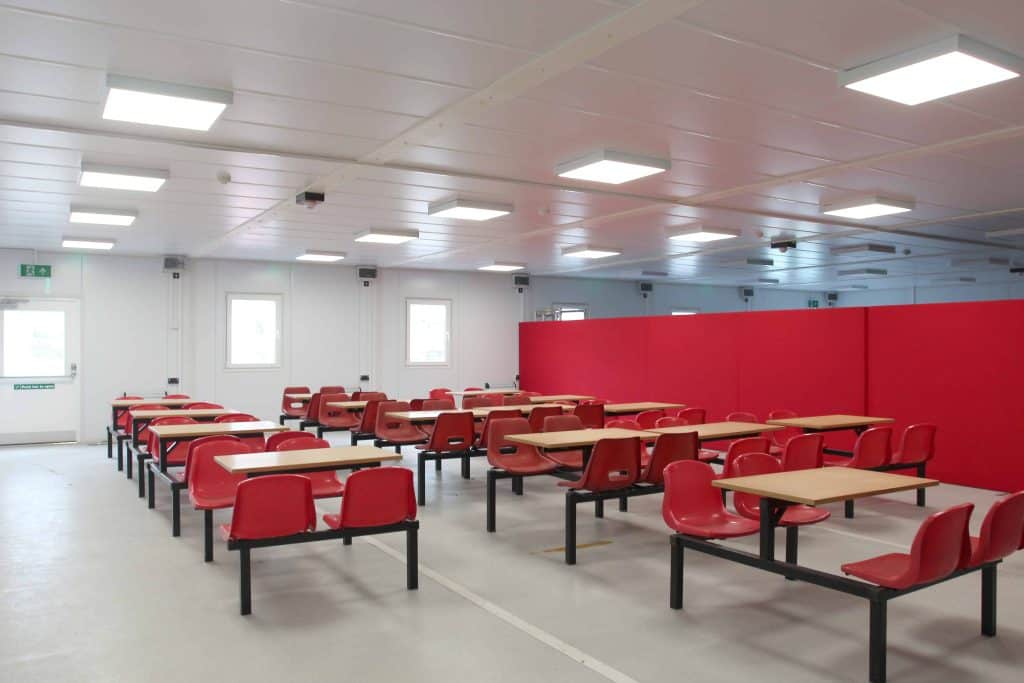
Efficient programme delivery based on a collaborative approach
With modular building, clients have the option to quickly deploy high-end, custom structures thanks to a flexible design to handover process.
Designed to last for many years on important infrastructure locations, modular buildings are durable whilst possessing a low carbon footprint. Once their temporary function has been satisfied, they are able to be reused or configured, further reducing waste.
Leading civil engineering contractors and end clients can achieve sustainable project completion, without sacrificing on timeframes or quality, by utilising high quality, bespoke modular project offices, welfare facilities, ancillary buildings and residential accommodation, leading to a more sustainable future within the construction industry.
To find out more about our infrastructure offering, click here.
For more information about how we can help your business, get in touch.