Modular buildings are fast emerging as one of the best ways to reduce the staggering carbon footprint of the construction industry.
By the end of this year, modular methods of construction are predicted to be one of the most popular forms of building with the global market estimated to reach a value of $157 billion, according to PBC Today. As the 2050 deadline of the government’s Net Zero strategy nears, the move to modular offsite manufacturing is more important than ever if organisations are to restrict the detrimental impact traditional construction is having on the world’s climate.
The state of play
Currently, around 40 percent of the UK’s carbon emissions are linked to the built environment. The construction sector is solely responsible for 60 percent of the nation’s waste. In large part, this is down to the industry’s energy-intensive practices, from the production of materials like concrete, to the transportation and procedures involved in building a building.
Choosing to produce through offsite building solutions – ie in a factory instead of on a construction site – addresses a variety of existing issues. Using modular buildings reduces vehicle movements, congestion, and material waste, all of which contribute to the generation of emissions during a building’s early stages.
The modular effect
The ability of constructing with pre-manufactured modular units to limit a building’s carbon footprint should not be underestimated; according to Green Alliance, pre-manufacturing can reduce embodied carbon by 45 percent.
Some reasons for this are:
- Less embodied carbon
Materials used to manufacture a modular building’s parts are typically less carbon-intensive than those used in traditional construction. Timber is a good example of this – it has the lowest embodied carbon of any common modern building material and is frequently used in modular units.
- Less waste
The efficiency with which materials are used also reinforces the sustainability of modular buildings. Offsite manufacturing significantly cuts down the wastage experienced on construction sites by ensuring materials are used precisely, restricting remnant resources going to landfill.
A key part of Premier Modular’s practices is the optimisation of materials for each of its buildings – to the extent that each structure is fully recyclable and zero waste goes to landfill. Such efforts are supported by several recycling initiatives, which include sending wood waste to a local power station for biomass fuel and recycling plasterboard cut-offs back into plasterboard.
- Less transportation
Another factor improving the sustainability of modular units is the decrease in energy usage from transporting materials, equipment and labour to the site, as all building components are manufactured in one place. This reduction in energy consumption can also be taken further to the buildings themselves with the implementation of low and zero carbon technologies.
- Design considerations
Premier Modular uses its technical expertise to ensure renewable energy sources like solar heating systems, photovoltaics and mechanical cooling systems are incorporated into modular buildings where possible, to ensure maximum sustainability.
Taking sustainability further
As the first non-financial company in Europe to be ESG-certified, Premier Modular is dedicated to driving sustainable building approaches and lessening the footprint of organisations across the UK and Europe. From sourcing renewable energy to power its manufacturing processes, to optimising a building’s energy efficiency, the company is spearheading the sustainable transformation of the built environment.
In order to better support local communities and reduce the impact of modular buildings on the environment further, Premier Modular established a Net Zero Pathway. This pathway outlines multiple goals to keep the company on track with its sustainable commitments. Ultimately every Premier process and premises will be entirely net zero by 2035.
Alignment with these aims can be observed in each of Premier Modular’s projects but particularly so in the 15,000m2 buildings for HS2 which:
- Were tailored to the client’s specifications
- Used the natural sustainable circularity of the rental fleet. These 30-year life-span buildings were utilised for the five-year project period, after which they will be repurposed for alternative projects.
- Incorporated low energy lighting, PIR lighting sensors, low water consumption showers, dual-flush toilets, effluent tanks to reduce discharge into local drainage, and rainwater harvesting to provide water for site operations
- Exemplified the speed at which buildings can be sustainably manufactured with time spent on the project totalling four weeks.
Successfully delivering solutions with a high environmental performance requires constant evolution.
To support ongoing growth, Premier Modular partners with the Institute of Environmental Management and Assessment, which supports with resources and knowledge, enabling Premier to stay at the forefront of sustainable practices.
It is endeavours like these – to bring about a positive change to people and the environment through responsible building practices – which maintain Premier Modular’s position as a leader in sustainable construction and will help to curb emissions over the next decade.
Want to find out more about your next sustainable permanent or rental solution?
Explore our wide range of projects here.
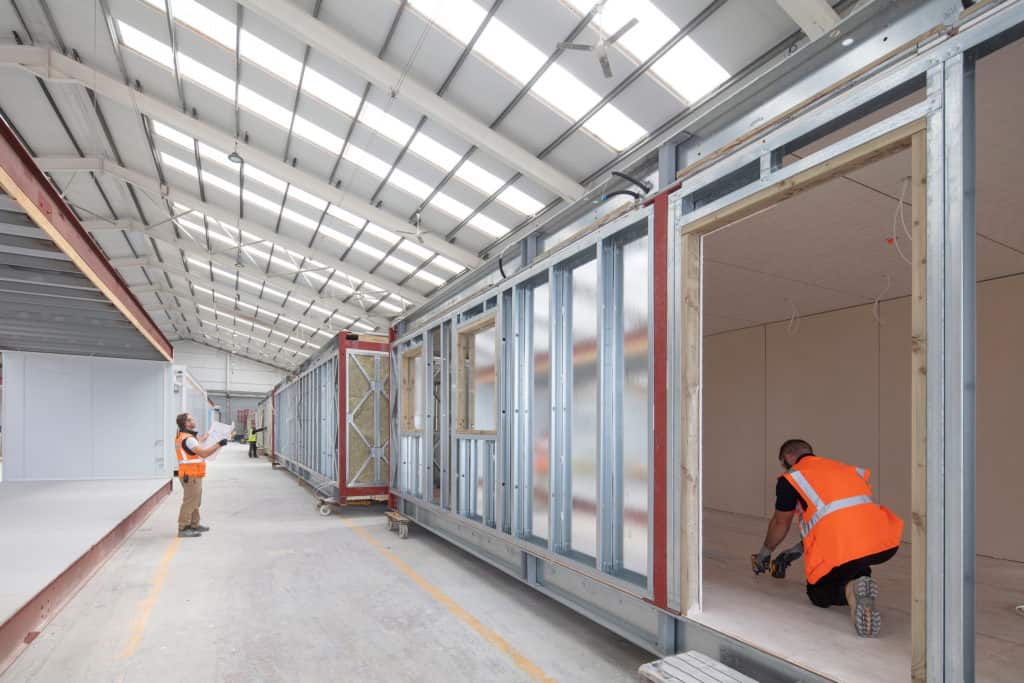
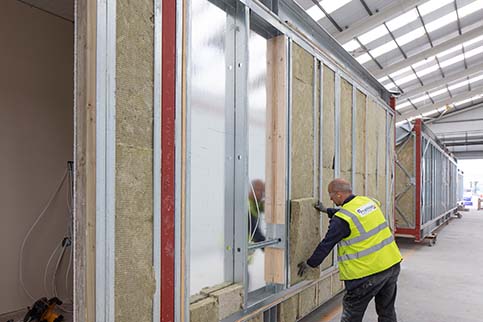