The number of university students increases year on year, however, for universities, student numbers often remain unconfirmed until the summer months, leaving any capacity constraints unknown until the very last minute. With decision makers sometimes left scrambling for solutions, many are turning to modular construction to alleviate some of this pressure, opting for high quality short or long term lease for facilities that can be delivered within tight timeframes.
Meeting the growing demand
As the number of undergraduate, postgraduate, home and overseas students continue to rise – reaching nearly three million last academic year – many universities need more space.
In addition to this, a steady growth in students taking STEM subjects over the last decade, combined with Rishi Sunak’s recent push for more STEM degrees, means that many new spaces must meet a variety of technical needs to ensure that they reflect the standards of the university.
Accelerated capacity solutions with flexible leasing…
- Speed of delivery
Modular construction is rapid. Whilst the groundworks and foundations are completed on site, the building is manufactured simultaneously in a factory-controlled environment offsite. This combination of onsite and offsite activity enables modular build programmes to often be completed up to 50 per cent faster than traditional build. Due to this streamlined process of offsite construction, buildings can be ready in as little as six weeks from the initial call to commission.
- Flexible leasing options
The uncertainty of yearly intake numbers can often be a key contributor to the requirement of additional space at such short notice. By choosing a modular building leasing requirements can be extended to best suit the client with long and short term options available.
- Complete in-house solution
At Premier, we have the expertise to take your building from design to completion, whilst providing a wealth of experience working with other contractors and organisations.
Whether a shell-only scheme or a full turnkey solution is needed, Premier will oversee the whole end-to-end process, including planning, groundworks M&E, testing and commissioning, to provide a high-quality, fast-tracked modular building solution that will deliver on all requirements.
- Future-proofed facilities
Modular buildings have the capacity to be adapted to suit changing needs and regulations. The flexible nature of the buildings mean they can be easily extended, reconfigured or repurposed should a university find itself needing to increase capacity, or space requirements change..
This reconfigurable nature not only supports the environmental targets of universities by eliminating the additional embodied carbon that a new building would produce, but also minimises the cost of future expansion plans.
Modular in action – how universities are thriving through modular construction
As modular construction grows in popularity, many universities have been utilising offsite construction to fulfil their student and faculty capacity requirements. Premier has successfully delivered a range of modular buildings that have rapidly expanded a university’s capacity whilst simultaneously meeting a variety of technical requirements.
The University of Hull: a sustainable IT facility integrated into the campus
In response to the UK government’s recent investment in STEM, the University of Hull wanted to ensure its education services and facilities kept pace with the latest advancements in technology.
To do this, the university required a bespoke, 850m² IT suite for its Data Science, AI & Modelling (DAIM) centre that visually integrated into its campus, its building management system (BMS) and existing infrastructure, whilst supporting the university’s net zero strategy.
The new two-storey facility would house the centre’s PCs and all associated wiring, which meant it needed a technical solution that would keep the building cool by accounting for the additional heat this would create. To solve this challenge, Premier Modular designed a mechanical ventilation system to optimise the internal atmosphere and ensure any generated heat was dissipated effectively.
Other energy-efficient measures included in the construction were:
- The installation of photovoltaic panels to reduce the building’s operational carbon.
- Constructing the facility from reconfigured existing module components, minimising the embodied carbon of the building.
These measures led to the building achieving an EPC rating ‘A’; supporting the university’s aim to become carbon neutral by 2027.
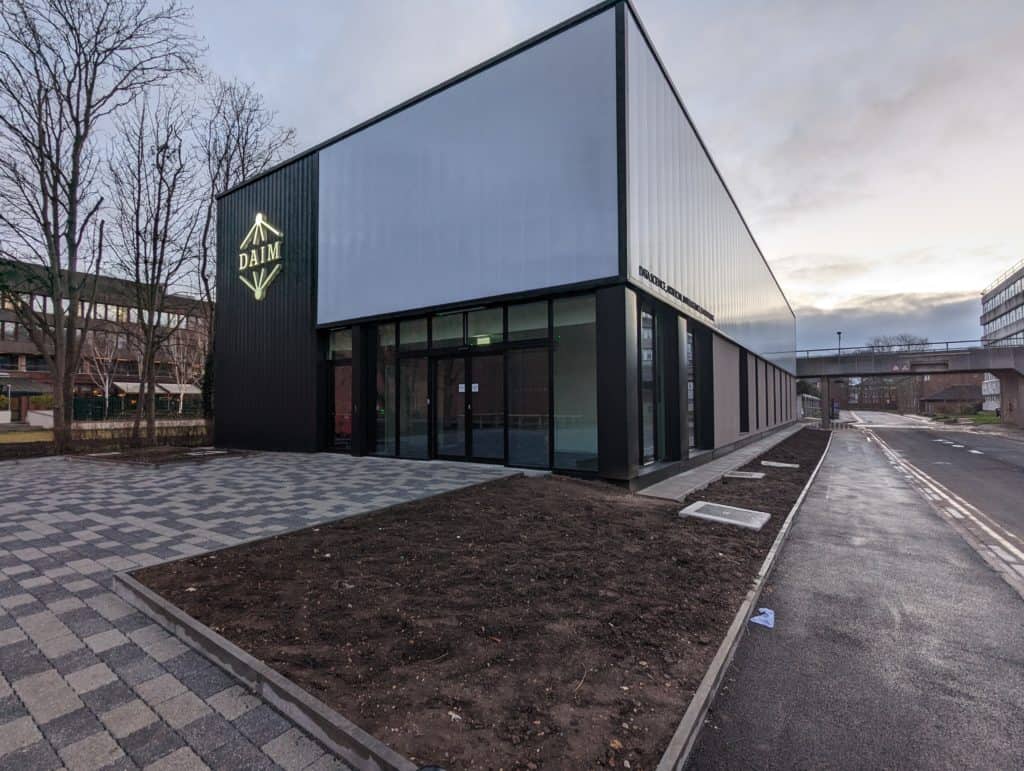
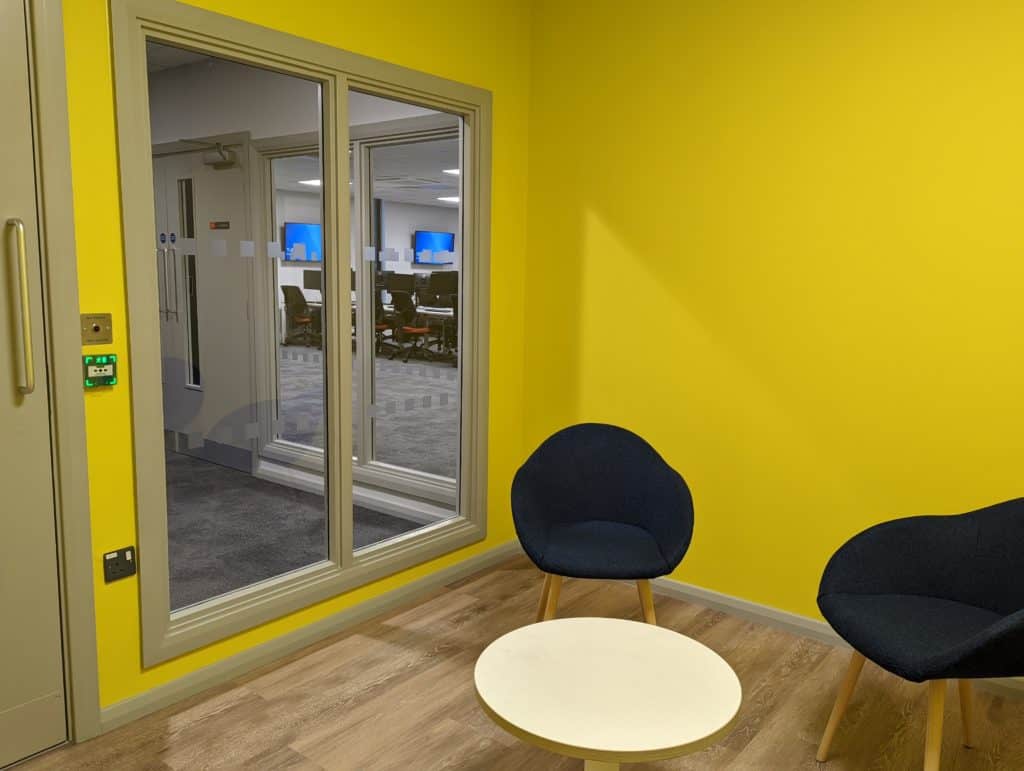
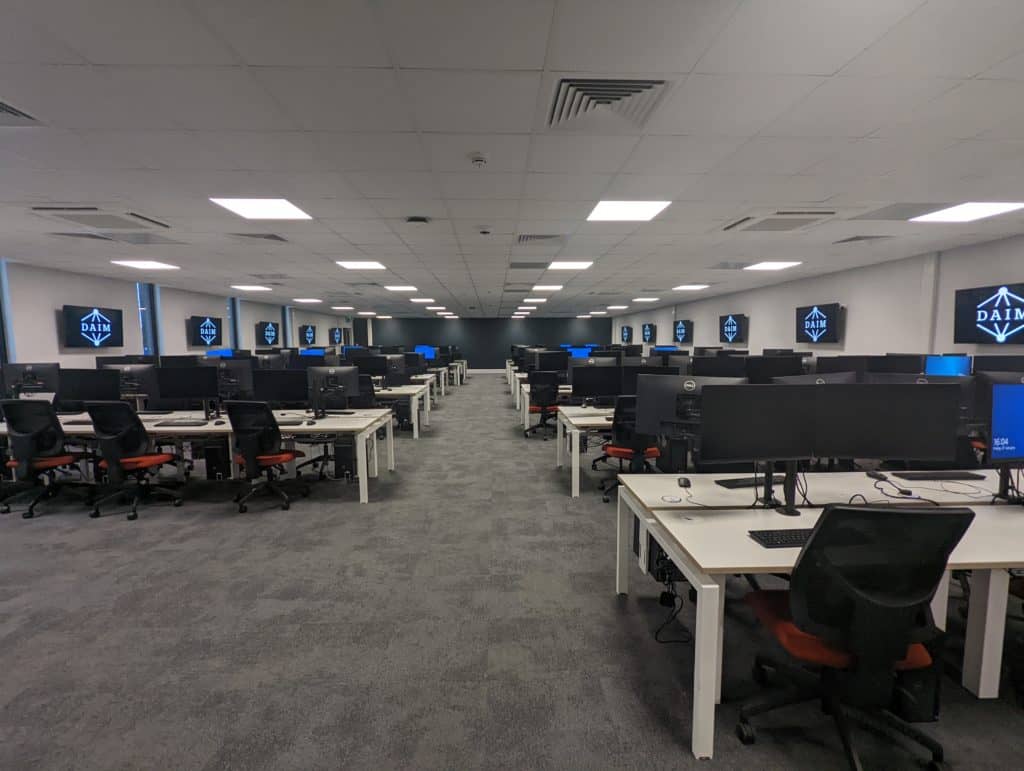
TEDI-London: a transformative, futureproofed engineering institute
The Engineering and Design Institute London (TEDI-London) required a long-lease facility to support its vision to continue to provide transformative engineering education for the next seven years, until it relocates to its future, permanent home within Canada Water.
British Land, the project’s client, decided to use offsite construction to create a modular campus, utilising a disused car park to reap the benefits of offsite construction.
The modules were engineered to provide a large, double-height space for exhibitions and events, along with a cafe. Four ‘maker-spaces’ encourage tenant collaboration and hands-on project-based learning as well as accommodating large-scale equipment, prototyping and 3D printing. Externally, a building corner was expanded to three storeys, creating a large roof terrace.
TEDI’s sustainability benefits included:
- Zero waste going to landfill during its manufacture offsite.
- Siberian larch cladding that can be re-used or recycled.
- A futureproofed building with modules that can be reconfigured, relocated or re-used when the 7-year hire is complete.
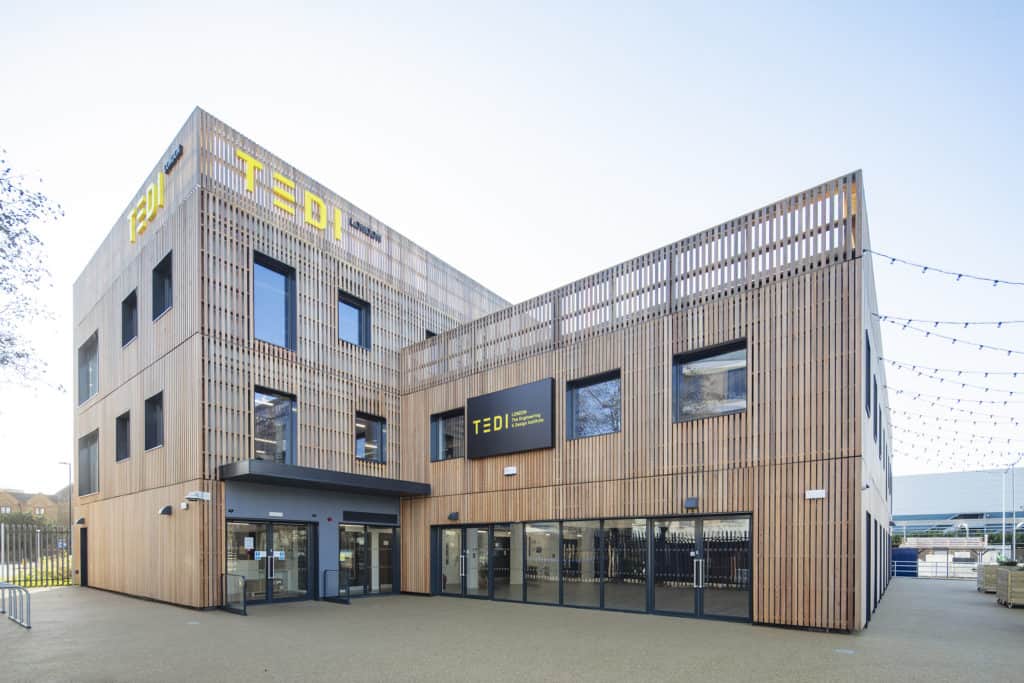
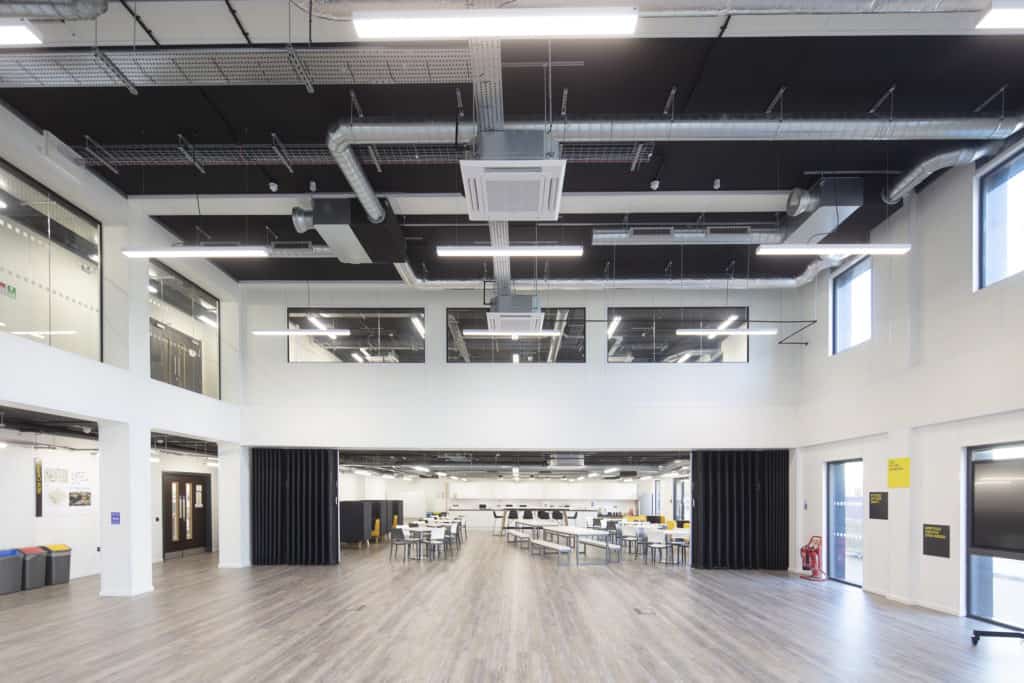
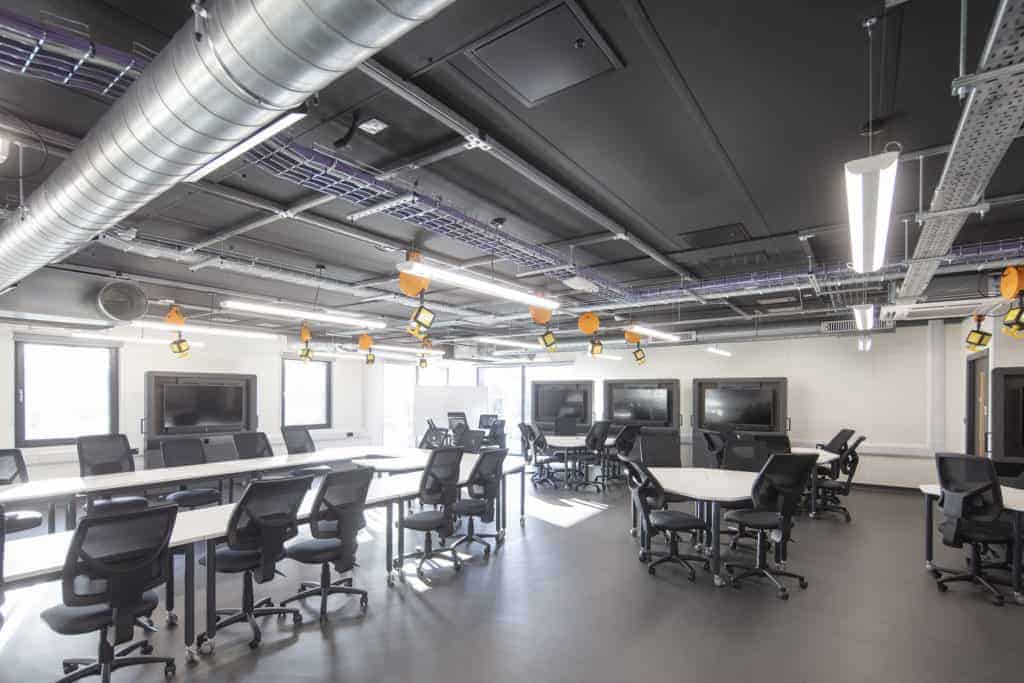
The future of construction is modular
With net zero targets fast approaching, embodied and operational carbon are under the microscope when it comes to the next generation of buildings. It’s crucial that we get it right now, across industries to ensure a sustainable future.
Not only are Premier’s buildings easily recycled and adapted to meet educators’ ever-changing needs, but independent engineering firm – Mason Clark – has verified the robust standards to which Premier Modular’s fleet is built – demonstrating that whilst some might see construction as stuck in the past, we have our eyes fixed firmly on the future.
To find out how you can enhance your facilities for future generations with fast-tracked, sustainable solutions, get in touch with us here.
As featured on Build in Digital.