The Ministry of Defence (MoD) has employed Premier Modular to solve a range of challenges working through a DIO (Defence Infrastructure Organisation) JV with a range of tier one contractors – including Kier, Galliford Try and Balfour Beatty.
Working with contractors, Premier Modular’s teams have delivered multiple, high quality MoD projects using modern methods and offsite building techniques.
Premier’s projects on behalf of the MoD serve a variety of purposes:
- Living accommodation
- Working environments (such as offices and workshops)
- Training facilities.
Compared with traditional in-situ construction methods, offsite ensures buildings can be bespoke manufactured or standardised to suit the client brief. They are also safer, as there is less work carried out on site, faster to install and of a higher quality.
The use of modular buildings allows the foundations and build to be carried out simultaneously. This ensures that the construction period can be dramatically reduced in comparison to the traditional bricks and mortar construction methods. Because the buildings are constructed in a factory, they’re not reliant on favorable weather conditions, thereby reducing delays on site and ensuring programme times and quality are maintained throughout the process. Without the weather delays, budgets are more controllable.
Fewer personnel on site and fewer deliveries also result in fewer health and safety risks and issues. Innovative lifting frames reduce the risks from working at height, ensuring staff are safe and secure throughout construction.
Working with agility and efficiency
Installing up to 10-bedroom modules per day reduces the disruption on surrounding areas and residents – this is particularly relevant when working on military establishments, as it supports the tight programmes associated with this type of contract.
Using offsite construction reduces the amount of time and number of subcontractors needed on military bases. As large portions of the schemes are completed in the factory programme, health and safety risks are reduced and security levels are less at risk. Modules are installed using a slick process, thereby reducing time and disruption required on site.
Offsite building programmes tend to come in on time and on budget, in comparison to traditional methods – which are prone to fluctuations in delivery and weather. That confidence springs from robust factory processes, governing the manufacture of modular units and therefore producing high-quality buildings – for both temporary and permanent applications – time after time.
Case study: RAF Chicksands
As a part of the Project SLAM (Single Living Accommodation Modernisation) initiative, the MoD needed to provide accommodation on RAF bases across the UK.
Premier Modular built the Chicksands SLAM project in its factory, based in the East Riding of Yorkshire, which was then delivered to the site in Bedfordshire, whilst the foundations were readied for the installation.
Each module was installed into the RAF Chicksands SLAM, with Premier’s innovative lifting frame and carousel. This specialist, offsite equipment enabled the installation team to easily adapt multiple module sizes. The frame has been acknowledged as best practice, globally, by Debut Services Ltd – the JV responsible for delivering thousands of SLAM bedrooms across the MoD.
To ensure maximum worker safety, Premier Modular’s innovative carousel sits on the roof of a module and allows workers to operate safely because they no longer need to hook up to the crane – which does the main lift – with a lanyard. The carousel has safety access gates that allow operatives to access the module roof when the module has landed.
Workers are then able to carry out key activities independently, without the need to rely on safety harnesses the entire time, setting an industry-leading standard for safety and efficiency.
Delivered in 11 weeks, this project provided much-needed accommodation for senior non-commissioned officers (SNCOs). The three-storey building comprised 42 modules, including 36 en-suite bedrooms and ancillary rooms.
The MoD’s partners chose Premier Modular because of its strict logistics, which adapted to the MoD’s particular needs and reduced programme times. Premier Modular’s module installation on RAF bases was scheduled so as not to interfere with military operations.
As a result of Premier’s achievements working with the MoD in terms of reducing procurement and programme times and costs, Premier is now accredited under numerous public sector frameworks, including the Crown Commercial Service.
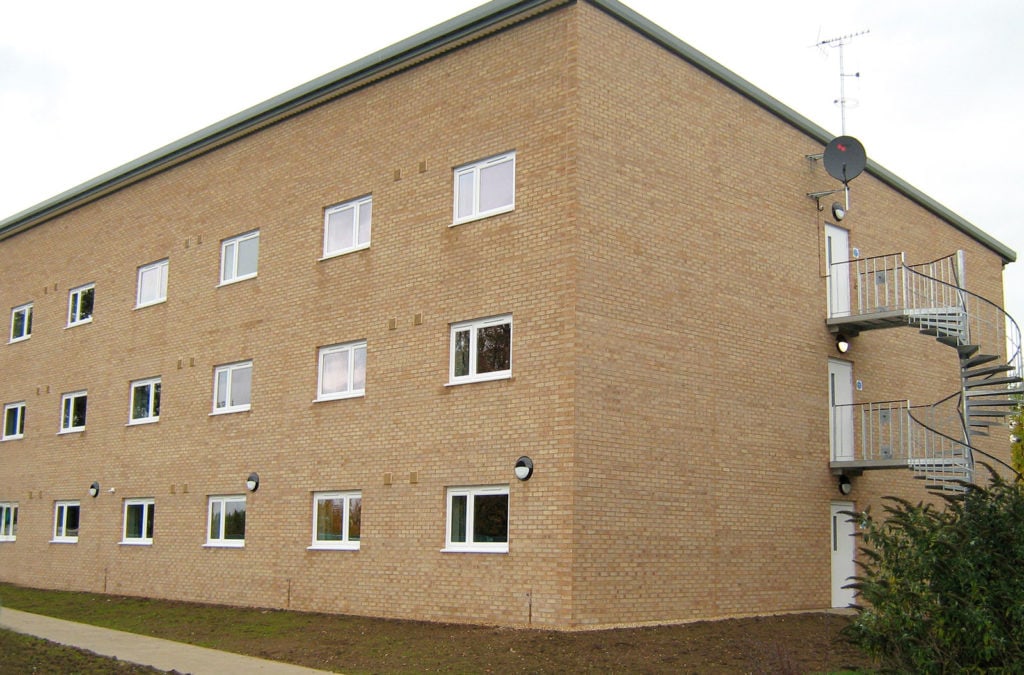
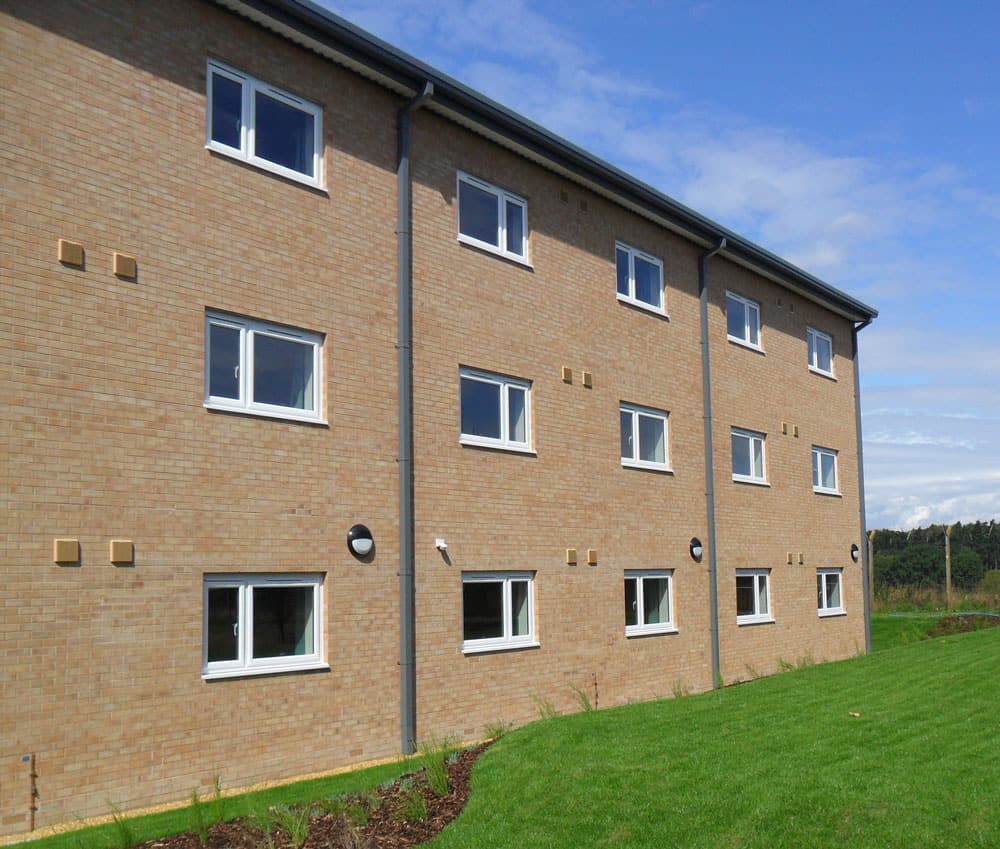
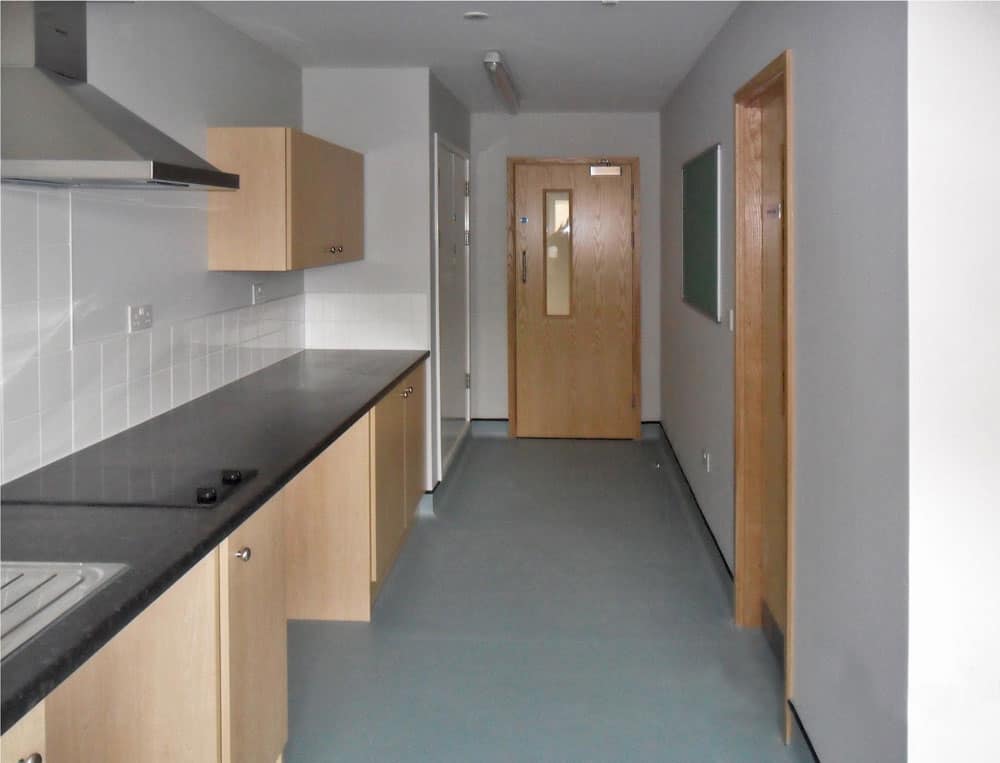
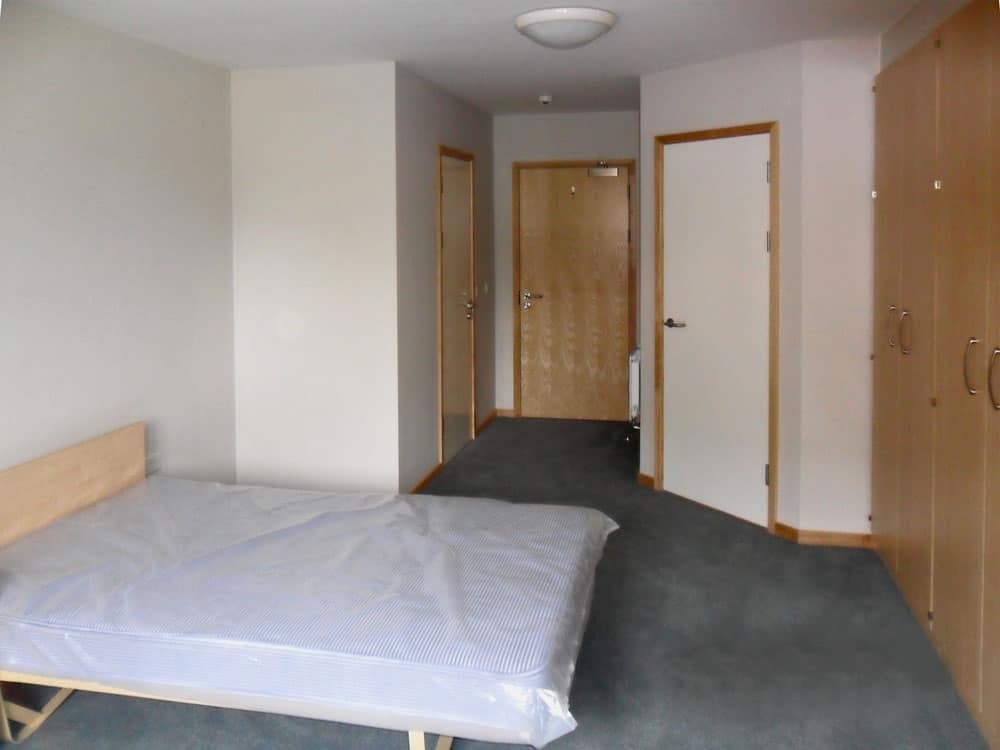
Offering bespoke building solutions
The variety of bespoke buildings Premier Modular has built offsite for the MoD include:
- Training rooms
- Operation rooms
- Archives
- Locker rooms
- Accommodation with:
- ensuite bathrooms
- laundry
- communal kitchens
- bike storage.
Case study: RAF Beacon Barracks
The MoD’s tier one contractor – Lendlease, chose Premier Modular as its supply chain partner to develop six modular accommodation blocks, each housing 72 beds a total of 432 bed spaces – at Beacon Barracks for ‘JRSLAs’ (junior rank, single living accommodation) as part of the military rebasing programme for staff returning from Germany.
The whole scheme was produced at a rate of 20 bedrooms per week to maintain the project target.
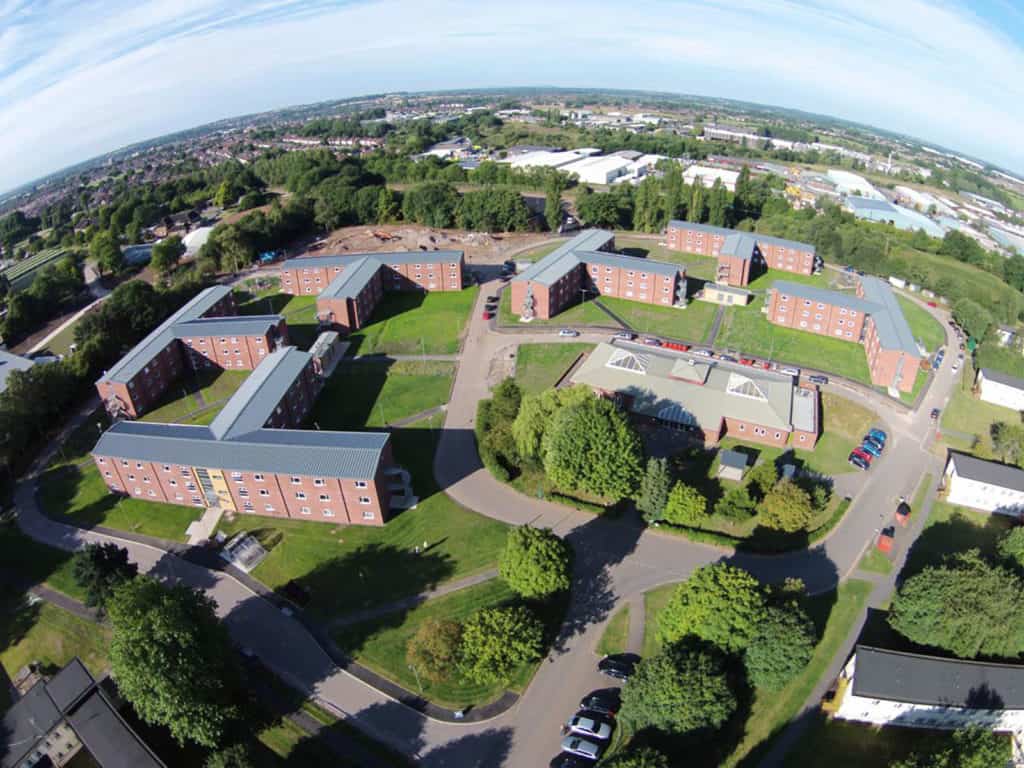
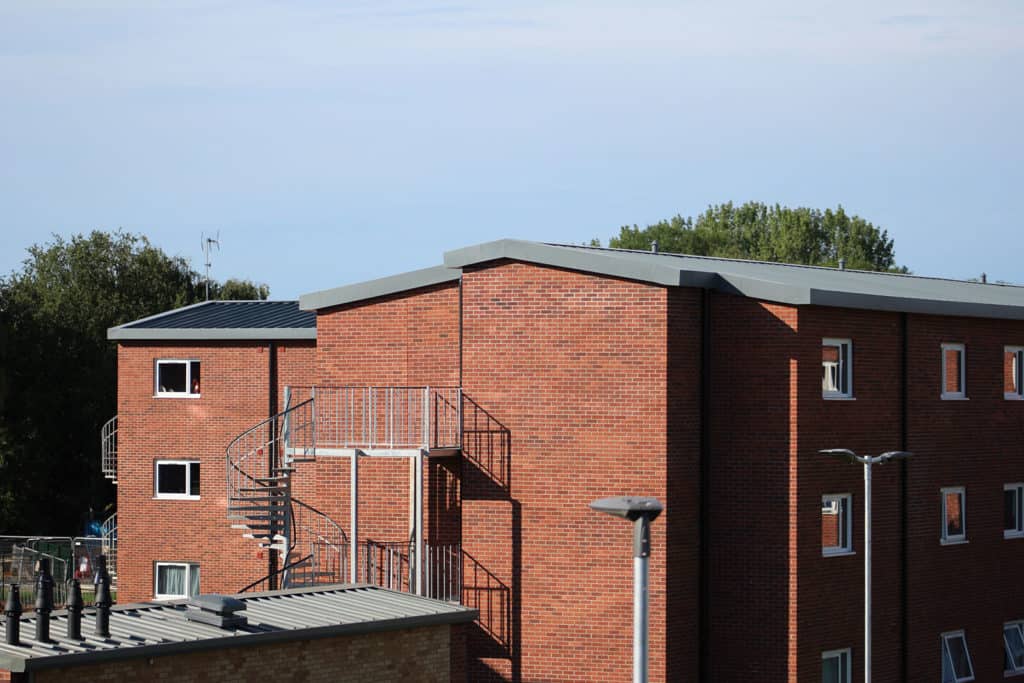
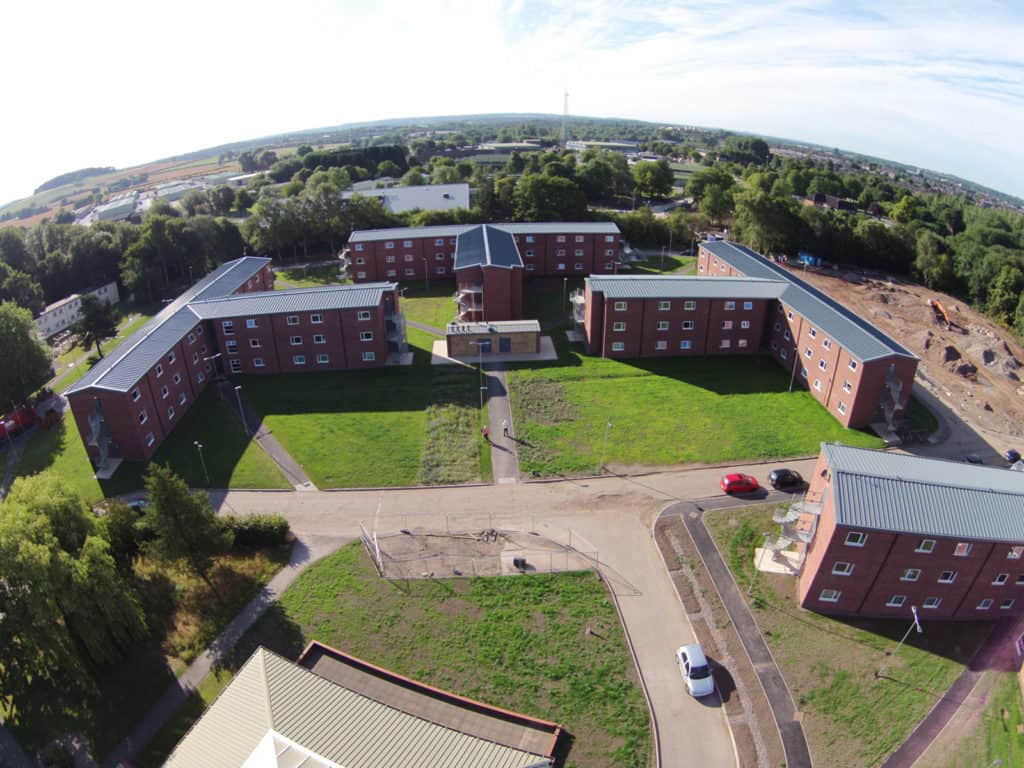
Case study: RAF Coningsby
BAE Systems, which provides aircraft services and products to the MoD, required a bespoke, purpose-designed accommodation wing to house the overseas aircraft technicians while they were being trained for two years.
The £2.6m temporary accommodation block comprises:
- recreation rooms
- a prayer room
- cloakrooms
- laundry.
- 66 bedspaces
To facilitate the new squadron on the site Premier Modular also delivered a permanent, bespoke £9m headquarters at RAF Coningsby which was signed off defect-free.
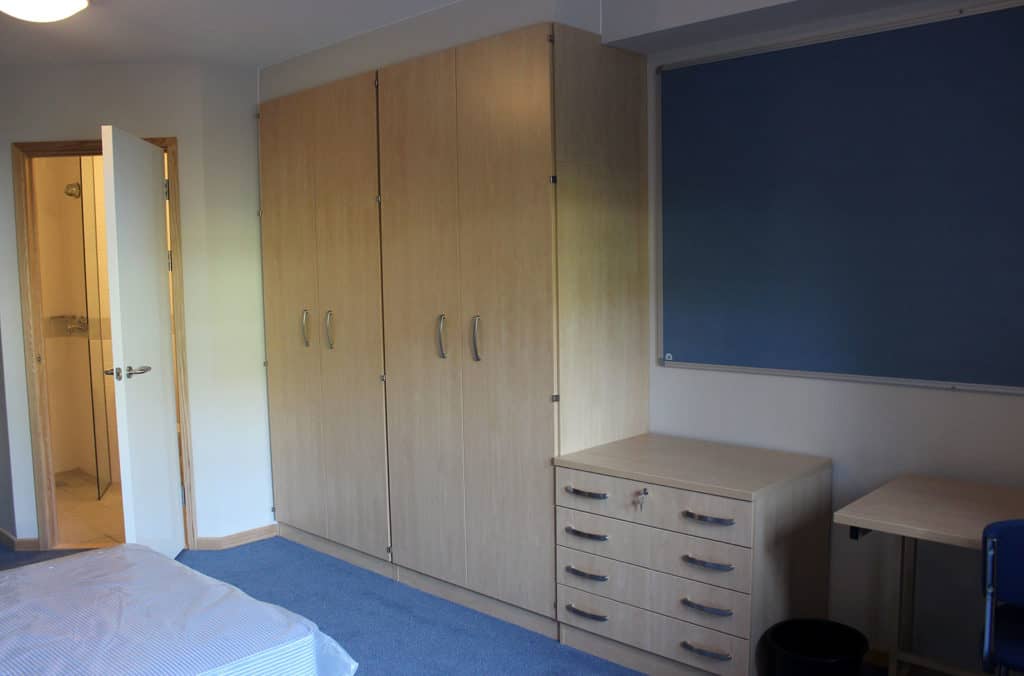
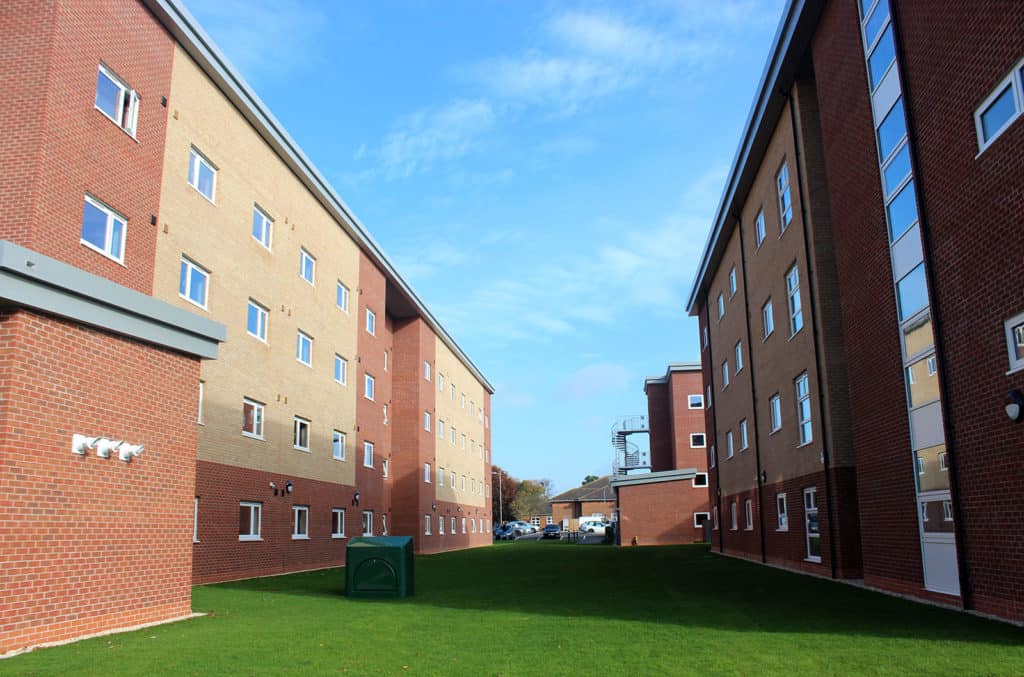
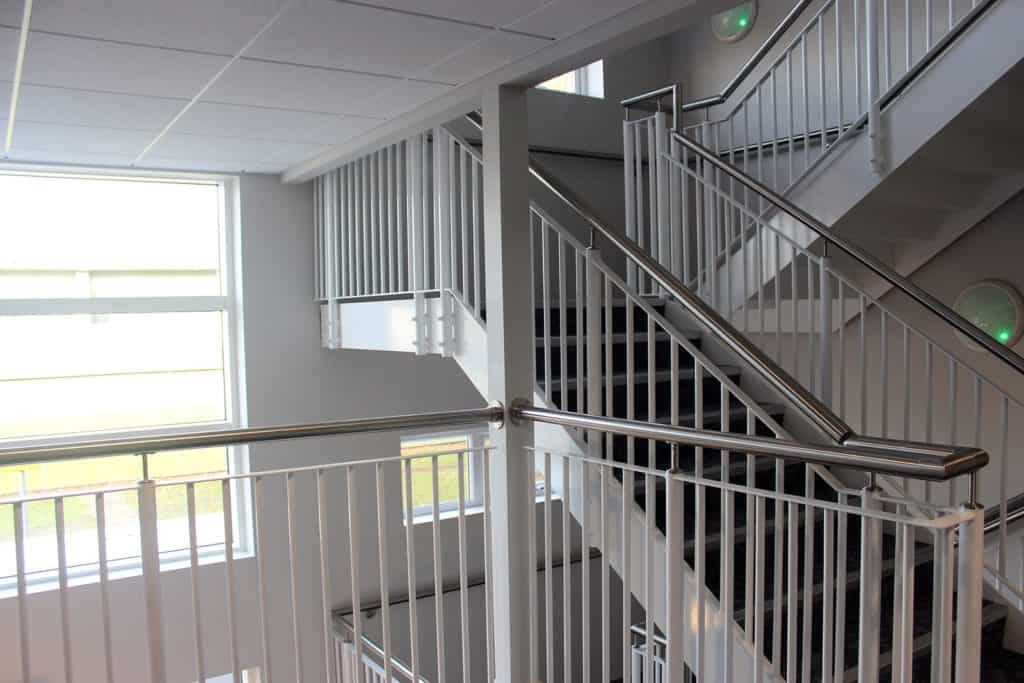
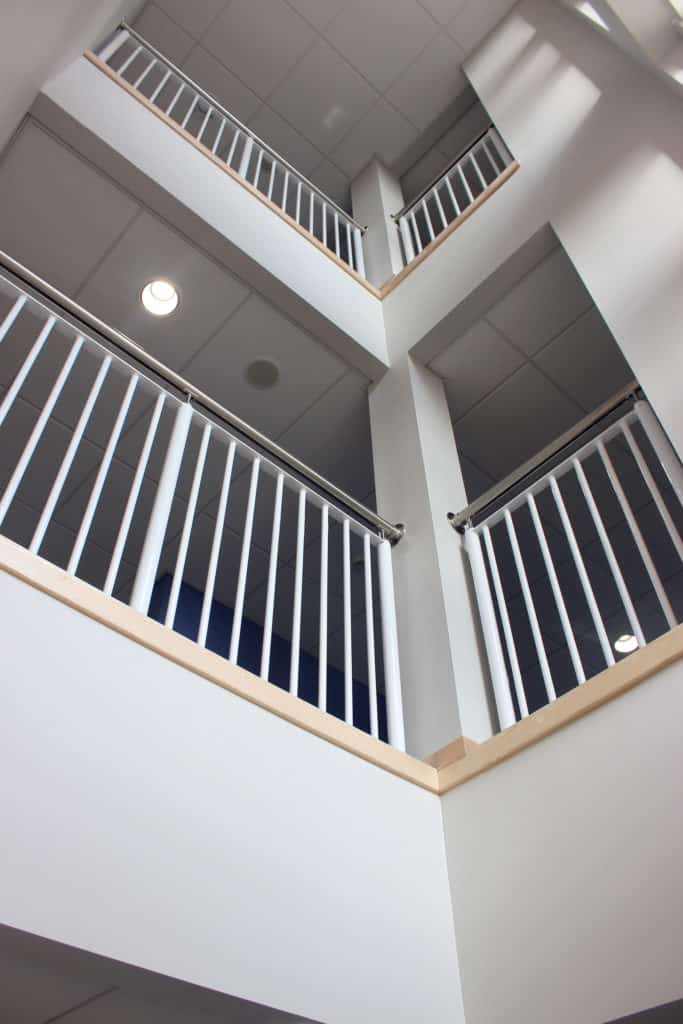
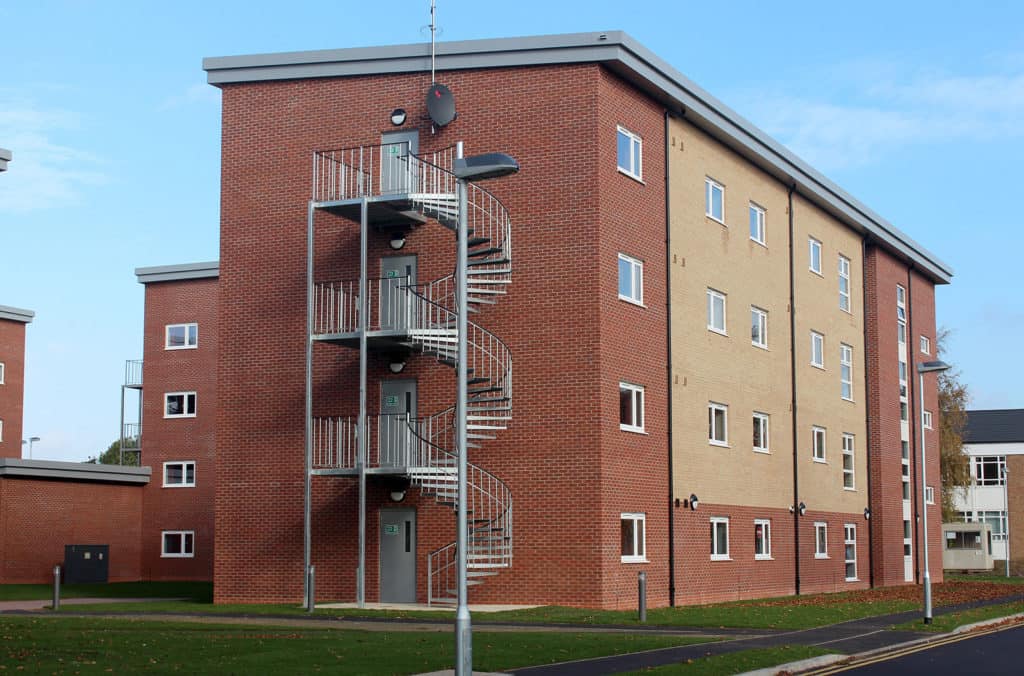
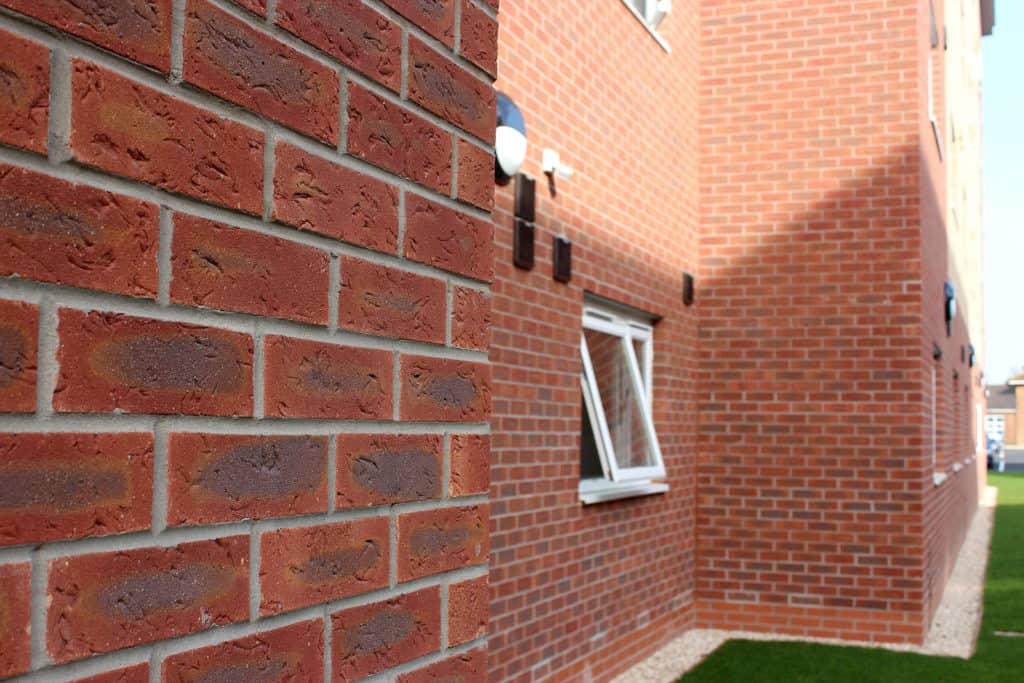
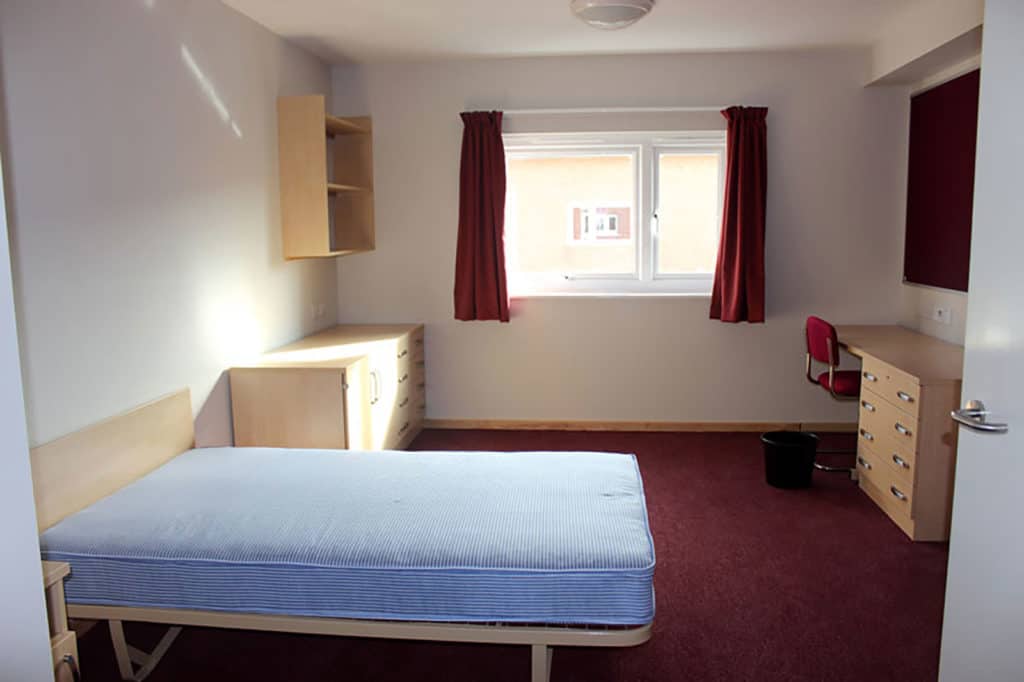
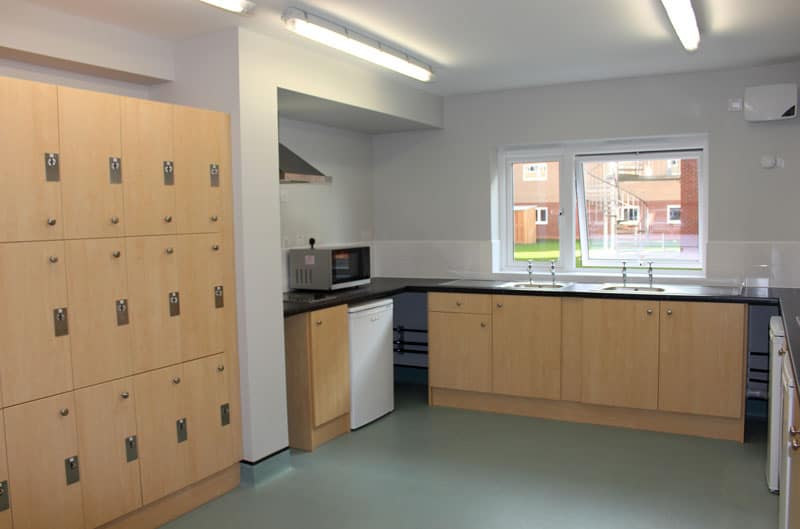
Financing offsite buildings
Premier Modular’s buildings can be purchased, leased or supplied for short and long-term use. This means modular accommodation can be easily reformed, removed and repurposed as things change.
Manufacturing with low carbon operations
Offsite construction is cleaner and safer than traditional bricks and mortar building.
There are fewer construction vehicle movements to and around the site and therefore less disruption for both the client and its site’s neighbours.
Lean manufacturing a building offsite also minimizes material waste as you have tighter control over the process. All Premier Modular buildings are manufactured with zero waste to landfill and offer many sustainability features, including improved U values, reduced air leakage, solar panels and air source heat pumps, therefore moving the buildings towards net zero carbon levels.
All Premier clients can achieve BREEAM excellent ratings, thereby reducing any construction project’s environmental impact.
Adding value throughout the process
Right from the start, the MoD team works with Premier Modular to get the design right. Premier constructs a prototype ie a bedroom in its factory. The MoD then reviews that prototype to finesse the details before full scale production starts.
If the MoD wants a turnkey project – to minimize client procurement time or for any other reason – Premier also supplies and installs fixed and loose furniture and fittings such as shower rooms, carpets and doors.
People and buildings performing in a high security environment
By their nature, military bases operate under the highest security standards in the world.
This requires design and build quality beyond thinking about toughened glass windows and enhanced steel structures. Above all, it means the Premier team must regularly pass the most scrutinous tests and be able to work with the strict discipline required.
Disruption on site is never welcome but is particularly critical when ordnance is on-site. That’s why modular offsite building – delivered by a disciplined team – works so well for the MoD.
Find out more about our MoD projects here.
Do you need support with the manufacturing of your modular building?